When taking the subway enroute to Chinaplas, the large-scale display of Arburg is very visible and definitely catches one's attention. At A41 booth in Hall 5.1, with focus on digitalization, Arburg showed the Chinese audience a new customer portal, the potential of Augmented Reality (AR) in the service industry and digital assisted systems.
“Digital transformation is the focus of our attention for many years,” said Gerhard Böhm, Sales Director of Arburg's Germany headquarters. “Our main purpose this time is to show customers how to use Arburg's innovative solutions to serve injection molding, with special attention on additive manufacturing and automation, and how to cope with the digital future of plastics processing," according to Mr. Böhm.
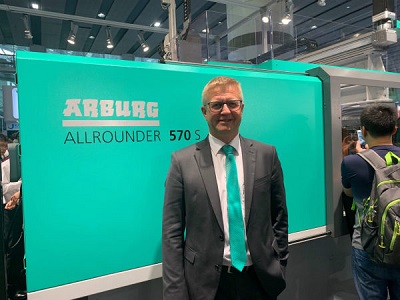
Mr. Gerhard Böhm, Sales Director, Arburg, Germany
Arburg has more than 30 years of expertise in IT networked manufacturing, which makes it easy for the company to move into the digital arena. From digital-assisted software packages to preventive maintenance and remote services, from the new portal service website to the company's own MES system, as well as the central production management system ALS, Arburg shows off all aspects of IT networking and more efficient production of plastic parts.
At CHINAPLAS, visitors witnessed how all machine exhibits on the stand were connected to ALS. The three main products include: a liquid silicone rubber processing system for the production of ready-to-use LSR/LSR watches, a gold-plated motor Allrounder for medical technology, and a Freeformer 200-3X for industrial additive manufacturing. All three machines are networked via the Arburg Central Production Management System ALS.
The site was subjected to the most onlookers of the two-component liquid silicone rubber processing system, and Arburg showed how to “make a molded” LSR watch. The hydraulic two-component Allrounder 570 S has a clamping force of 220 tons and two injection units arranged in an L-shaped position, which automatically produces two two-color straps in a 70 second cycle time. The strap is removed using a linear manipulator system, the Multilift V 15, which is placed in a cooling station and an assembly station. Complete the final case and buckle installation to become a “ready-to-use” watch.
In addition, Arburg's partner Mehow exhibited a hydraulic two-component Allrounder 470 S on the B81 stand in Hall 5.1, using PC and LSR to produce water cups. On the other side of the stand, the Allrounder 370 E Gold Edition motor is producing a PC breathing mask. It has a clamping force of 60 tons and is used to produce children's breathing masks.
In the additive manufacturing exhibition area, Arburg's Freeformer processing system is also receiving attention: the system can open raw materials openly, and Arburg's plastic moldless molding technology (APF) brings greater to the plastics processing industry. Material freedom. Users can process their own raw materials, or they can independently optimize the size of the gobs, using ordinary plastic particles for injection molding. On the basis of the Freeformer 200-3X, Arburg has added a large three-component machine, the Freeformer 300-3X, which can realize a two-component hard/soft-bonded AM component. In addition, the new Freeformer offers more space and higher temperatures, and is automatically integrated into a networked production line.
Nike Air Max 97