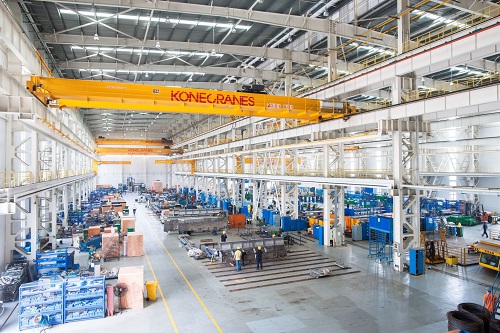
Konecranes, a Finnish company specializing in the manufacture and service of cranes and lifting equipment, has implemented Siemens’ digital innovation platform to accelerate its product development process and connect product and performance data together. The company is using MindSphere, the open, cloud-based Internet of Things (IoT) operating system, and the Teamcenter® portfolio, the world’s most widely used digital lifecycle management software, to leverage the digital twin and reduce the number of physical prototypes, which helps to increase efficiency and decrease product validation time. The Konecranes proof of value is one of the first implementations of IoT to develop a framework that connects and synchronizes the virtual (engineering design, analysis and simulation) and physical (testing and operational reliability) worlds.
“The product design process is currently based more on an engineer’s experience and generally shared assumptions than measured facts from existing products,” said Juha Pankakoski, Executive VP, Technology at Konecranes. “These assumptions often lead to non-optimized designs that are over engineered. With an integrated digital twin platform, we see major potential in speeding up the product development process, reducing prototypes, increasing traceability and thus improving quality and reduce development cost.”
Today design, simulation and prototype testing organizations operate in their own silos, often using out of date processes for their work. At Konecranes, a digital twin was utilized as the communication approach between all three organizations to review data and provide feedback around engineering, simulation and testing intent. Using the Siemens platform for digital innovation, Konecranes has been able to connect the data from all of these organizations to create one 360 degree view of how prototypes are running and performing, and correlating requirements to, real world performance data. A closed-loop digital twin framework using IoT and product lifecycle management (PLM) technologies can lead to faster design issue resolution and shorter prototyping phases by leveraging virtual sensor data in product simulations to provide accurate results. It can also improve overall quality and a support downstream product lifecycle processes.
“Bringing together assets from both the physical and virtual domains provides a seamless framework of business data which can help eliminate rework, leverage factual data surrounding prototypes, and provide closed-loop feedback regarding physical and virtual assets,” said Tony Hemmelgarn, President and CEO at Siemens PLM Software. “The proof of value of the digital twin achieved at Konecranes confirms the business value of integrated IoT and PLM technology. The power of the Digital Twin connecting MindSphere IoT real time data to the virtual engineering assets in a seamless user experience turns generated data into actionable information to create a closed-loop decision environment for continuous optimization.”
Nike Air Max 2017