An exclusive interview with the Sales Manager Eric Kuo of Dipo Plastic Machinery Co., Ltd places emphasis on the company’s strengths and how it has become a leading bag-making machines and blown film machineries manufacturer for over 30 years. Eight years ago, the company started to develop its own brand ‘Dipo’ with a strong focus on environmentally-friendly bag making machines to assist users who are highly involved in the manufacture of products out of bio-degradable materials. At Taipei Plas this year, the company will demonstrate its innovations. Prior to the exhibition, Mr. Kuo discussed what a new plastics economy means to bag-making machine manufacturers like Dipo.
Eco-friendly plastics as top goal
Dipo’s recent cooperation with a customer engaged in the production of biodegradable bags has led it to develop more appropriate production system. Mr. Kuo pointed out that this particular customer has successfully produced biodegradable bags that met the EU certified standard of Compostable Plastics EN13432 and the US standard ASTM D 6400-04. “These plastics materials would contribute to the applications in biodegradable bin bags, agricultural films and packaging films. Dipo’s role is to redesign each machine’s mechanical property and feature for the machine to fit for certain use. Thus, it has taken 7 years for a high-end green bag making machine to be born”, explained Mr. Kuo.
When asked on the challenges in promoting biodegradable plastics materials, Mr. Kuo said the reasons for those who are still holding back from using greener plastics solutions can be attributed to the higher price of biodegradable raw materials and also the limitation of longer storage time for such materials. Therefore, he is pushing for a wider recognition in the governmental level as well as the educational arena to achieve fundamental conceptual understanding, if not acceptance on green plastics economy. The biodegradable products produced from Dipo’s machine are at present running testing trails in the UK; the next steps in the future will be to conquer the barriers of long-distance shipping biodegradable materials, and abiding with different plastics standards across the globe.
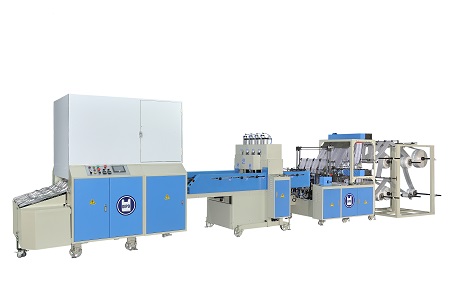
Legacy generates fresh innovation
Mr. Kuo reflected on the early days when his father established Dipo: “The greatest change in bag-making machines today focuses on the personalization trend, which is essential for giving that extra value to clients.” Dipo has already upgraded all of its machines’ energy consumption level – moving from mechanical gears to frequency converter, and then presently equipping the machines with full servo.
Dipo also applied an intelligent system to print serial number on bags and an auto-packing system that radically decreased the labor needed during production. The intelligent serial number printing system has helped clients increase the quality of management and efficiency at the factory, while receiving accurate information and feedback on every batch of product quality. “This kind of unique competency is what we are aiming to create for our clients, and we would like to meet these kinds of buyers at TaipeiPlas this year!” Mr. Kuo explained.
Dipo has attended TaipeiPlas for decades and is familiar with the changes in the plastics industry. Now, there are abundant reasons for Dipo to advocate a new plastics economy and lead the supply chain leaping into a cycle of environmental-friendly plastics.