Royal DSM, a global science-based company active in health, nutrition and materials, brings its sustainable and innovative solutions aimed at meeting the major global challenges at CHINAPLAS 2018 in Shanghai, China. The company‘s booth, located at Hall 7.2, Booth number D71, focuses on its latest innovations in high-performance engineering thermoplastics and Dyneema®, the world’s strongest fiber™.
Visitors to DSM’s booth are introduced to the broad range of material solutions that meet present and future product development demands in the automotive and electronic industries. In particular, the company’s Connected Cars solutions is a reflection of the future of cars where all individual parts of the vehicle - under the hood, inside the passenger compartment, on the exterior - will be connected via smart electronic devices integrated within an overall “intelligent” design. Connected Cars will drastically change the way people drive, just as smartphones have changed the way people communicate. All are becoming part of the Internet of Things, IoT. Apart from this, New Energy Car is yet another rising trend. Through developing HV component, E-motor and battery for New Energy Car, DSM continues to scale new heights in material technology for the automotive industry.
As the key challenge for Original Equipment Manufacturers (OEMs) in this context will be the need to develop next-generation cars full to the brim with advanced electronics, lightweighting will be critical to meet the requirements for lower emission and fuel efficiency. This need to cut weight is even more critical when applied to electric vehicles, which today still have much lower range than cars powered by internal combustion engines.
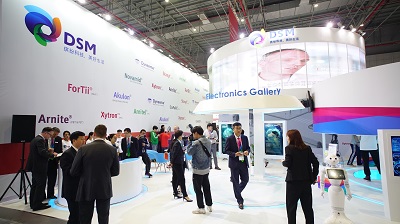
Moving forward in the Asian region
CHINAPLAS 2018 serves as an ideal venue for DSM to further promote its broad portfolio of high performance materials. As Matt Gray, Regional Commercial Director of DSM Engineering Plastics Asia Pacific, puts it: “China remains our most important market and with China continuing its growth path, our production facility here is moving forward in terms of capacity to address the demands of the market. The China market itself is experiencing rapid development especially with the implementation of various policies, including the “Made in China 2025” strategy and these will create opportunities for further innovations and expansion in the next 2-3 years.” Aside from China, Mr. Gray said that DSM has been addressing demand for important markets, such as India, Japan and other Southeast Asian countries.
In terms of product portfolio, four products are currently posting high demands – Stanyl®, ForTii®, Arnitel® and EcoPAXX®. Stanyl® is a high-performance polyamide 46 used for applications in automotive, E&E, gears and outdoor power equipment. ForTii® is a breakthrough high temperature polyamide with halogen-free flame retardant grades for demanding applications in the electronics, lighting, automotive, white goods, industrial and aerospace industries. Arnitel® high-performance ThermoPlastic Copolyester offers a unique combination of flexibility, high temperature resistance and strength - plus excellent processing characteristics. EcoPaXX® belongs to the family of long-chain polyamides, which offer exceptional performance in the most demanding of environments.
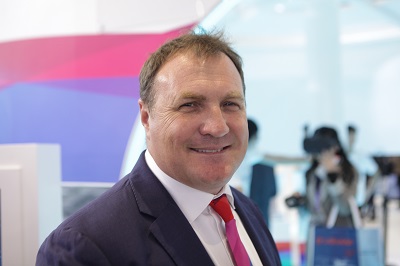
Mr. Matt Gray, Regional Commercial Director of DSM Engineering Plastics Asia Pacific
Bridging the gap in sustainability
The development of materials that meet the sustainability challenge has been a complex process that the market today has yet to fully embrace. “DSM has been innovating in this area, in fact, our EcoPAXX®, which is a material based on soybeans, is gaining popularity not because it is green but because of its mechanical properties and this is a different angle for us. We have also expanded our range of Arnitel® to include Arnitel® Eco, which is a bio-based thermoplastic copolyester,” according to Mr. Gray.
But the move towards this area may prove a difficult one because the market still does not have the ability to pay the premium that these materials demand and to be able to engineer them would cost more for the customer. “But we'd like to see that change and we are looking at other innovative ways to bring sustainability to the fore that we continue to work with innovative partners, fuelling our innovation and our ability to come up with these solutions,” Mr. Gray explained.