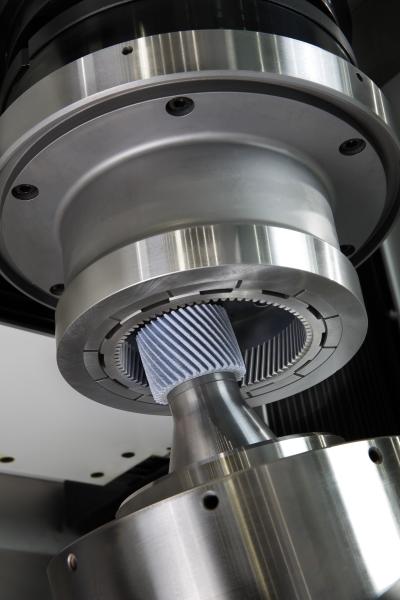
The DVS gearing specialist PRAEWEMA Antriebstechnik continues to expand its technological expertise in order to keep pace with the growing significance of planetary gear trains for automatic and particularly electric vehicles, with the associated need for even higher-precision production of toothed gear components. The company from Eschwege, North Hesse/Germany now offers holistic machining solutions for µm-precise production and optimization of both external and internal gearings. Here is a detailed look at the market and technology leader's extensive expertise when it comes to the highly complex production of inner-toothed ring gears for planetary gear trains.
Planetary gear trains are predestined for installation in the powertrains of automatic and particularly electric vehicles. Compared to conventional spur gear stages, the planetary gear train makes it possible to divide the power flow in three or more strands. This permits higher transmission and reduction ratios to achieve greater performance density, while reducing weight and package aspects and improving running smoothness. As a result, they fulfil the existing need for higher torques with reduced package and weight for electric drives that stand out with higher motor speeds of up to 17,000 rpm. In terms of production, these factors lead to narrower geometrical tolerances and thus the complex demand for even higher precision NVH-optimized machining of corresponding planetary gear train parts, referring particularly to the quality of necessary gearings. The DVS company PRAEWEMA Antriebstechnik in Eschwege fulfils these requirements with tailor-made technology, machinery and tool solutions for high-precision gear manufacturing and optimization.
Tailor-made solutions for soft and hard-fine machining of the simple planetary set
Based on a wealth of comprehensive expertise with its world-leading optimization technology known as PRAEWEMA gear honing for external gearing surfaces, the DVS gearing specialist has now refined this technology even further for the hard-fine machining of internal gearings. Supplemented by the use of the highly productive Power Skiving technology together with the possible integration of additional machining steps such as deburring, PRAEWEMA now offers an integrated package for high-precision soft and hard-fine machining of the simple planetary set – in other words, now also for inner-toothed ring gears as well as outer-toothed planetary and sun gears. While in the past inner-toothed ring gears were not expected to reach such high quality standards as outer-toothed planetary and sun gears, things have now changed as a result of current powertrain developments. There were two reasons for the lower quality standards in the past. On the one hand, tooth root bearing capacity is less critical than in planetary and sun gears due to the more favourable geometrical conditions. On the other hand, suitable highly developed machining technologies were simply not available due to the comparatively small batch sizes of rings gears.
Increasing demands for the production quality of ring gears
Up to now, manufacturers have enhanced the performance and NVH behaviour of planetary gear trains almost exclusively through continuous improvements to the machining quality of planetary and sun gears with a sequence of both soft and hard-fine machining processes. These parts therefore offer high gearing qualities and strength values, and allow for a large number of toothing corrections. By contrast, the inner toothing of ring gears typically made of tempering steel is usually just soft machined with no additional heat treatment as a rule after the gearing is finished. The result: limited correction possibilities and average strength values and toothing qualities, with a negative impact on wear and noise behaviour and thus on the functional efficiency of the powertrain. PRAEWEMA has identified potential for optimizing the production of ring gears. This demanded expertise not just in machining toothings but indeed in all process steps, and opened up scope both to enhance the load rating through case hardening and to use precise, economically efficient hard-fine machining procedures after the heat treatment phase. To this end, the company developed and optimized corresponding soft and hard-fine machining methods together with a suitable machine concept. Depending on the user's quality demands for the resulting ring gear, Image 1 shows possible process sequences for the production of ring gears. Variants 1 and 2 show the conventional manufacturing process described above; the nitriding heat treatment option in variant 2 improves the load rating but has a negative impact on toothing quality. Variants 3, 4 and 7 show process sequences that optimize both load rating and toothing quality. In each case, soft machining is followed by case hardening heat treatment. This hardening method, implemented for example by mandrel hardening or low pressure carburising followed by high-pressure quenching, may improve material strength but results in hardening distortion such as shrinking, ovality and ship-form (see image 3). Hardening then has to be followed by corrective hard-fine machining for important functional parts of the gear wheels, particularly the running gears and bearing seats.
Heat treatment improves strength but necessitates corrective hard-fine machining
Image 3.1 and 3.2 show a typical ring gear geometry for an automatic car transmission where the roundness and smoothness distortions were almost halved by specific process control of the hardening phase. Here due consideration must be given to the fact that a certain protuberance allowance has to be heeded during soft machining to prevent notches in the finished gearing. The quality requirements for soft machining can also be reduced within narrow limits due to the subsequent hard-fine machining. The same also apples to the possibility for toothing corrections. Variant 5 constitutes a stand-alone special case: here a pre-skiving process is followed by honing as part of soft machining in order to improve the surface quality. This process sequence deliberately tolerates the hardness distortion resulting from subsequent nitriding. When it comes to hard-fine machining, here the DVS company opts for highly productive Power Skiving, respectively the PRAEWEMA gear honing that has been specially refined for inner gearing applications. Hard Skiving permits effective correction of hardening distortions without the characteristic feed marks. It is therefore suitable for the mass production of ring gears with slightly lower quality standards (variant 3) as well as a pre-machining for gear honing, as only very limited further material removals are necessary to minimize form deviations and pitch errors, thus achieving very high gearing qualities (variant 4). In variants 6 and 7, soft machining using Power Skiving and heat treatment with nitriding or case hardening is followed by hard-fine machining using inner honing of the soft machined gearing. The latter variant is given preference for ultra-high stressed parts in view of the better load rating properties.
Highest surface and profile quality for internal gearing surfaces
Just like the proven honing for external gearings, PRAEWEMA's refined gear honing for internal gearings fulfils the highest standards for surface and profile quality of toothed parts so that ring gears can now be machined in hitherto unequalled productivity and manufacturing quality. The typical gear honing structure has a positive impact on the excitation characteristics of the gearing. Image 2 clearly shows the minimizing effect on both surface structure and the parameters influencing noise and wear development, respectively pitch deviations. Powertrain manufacturers can therefore produce wear- and noise-reducing planetary gear trains with higher transmissible torques, exactly in line with the demands made for application in the powertrains of automatic and particularly electric vehicles. Economically efficient and precisely fitting original tool solutions for this process are available from the DVS affiliate DVS TOOLING, whose range covers the entire scope of tools needed for PRAEWEMA gear honing. This includes the completely new development of inner-toothed VarioSpeedDresser tools and outer-toothed honing wheels. As with the honing of external gearings, the VarioSpeedDresser also permits precise dressing of the honing tool, or in this specific case the honing wheel, with a defined cutting edge and flexible definition of the tooth geometry. In combination with PRAEWEMA gear honing, it is thus possible to make geometric adjustments respectively flank line corrections while at the same time applying exact finishing to the gearing surfaces. As such, it comprises a milestone in the field of hard fine-machining of hardened internal gearings of gear components.
Adidas