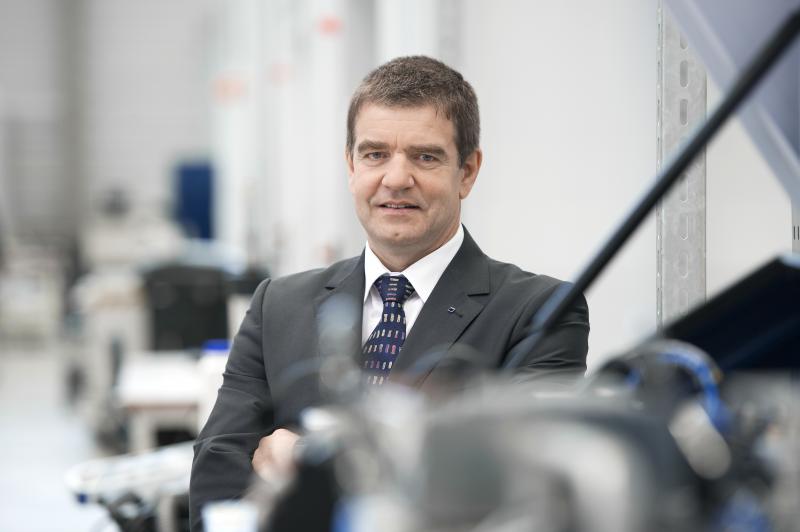
“The German machine tool industry is setting one production record after another.” With this good news, Dr. Heinz-Jürgen Prokop, Chairman of the VDW (German Machine Tool Builders’ Association), Frankfurt am Main, opened the organisation’s annual press conference. In 2017, the sector achieved growth of four per cent, and will thus, according to the provisional results, reach a volume of around 15.7 billion euros. For 2018, the VDW is expecting production output to increase by another five percent.
In 2017, once again exports proved to be the primary driver involved. 71 per cent of German machine tools were sold abroad. Exports rose by eight per cent to reach 10.1 billion euros, excluding repairs and maintenance. Domestic orders fell during the same period by three percent.
The major boost to German exports came from America, with an increase of one-fifth. Brazil and Mexico reported significantly overproportional rises. There was also a gratifying performance by the second-most-important machine tool market, the USA, which with growth of likewise one-fifth is precisely in line. “This means the USA’s economy is investing, and we as equipment suppliers are participating in the benefits. Because without machines from abroad, also and especially from Germany, the USA’s industrial sector cannot regain its competitiveness on the global market,” says Heinz-Jürgen Prokop.
German exports to Asia staged an impressive recovery last year. This is primarily attributable to the lead market of China. The reinvigorated demand produced export growth of almost one-fifth. In its wake, the entire region is experiencing an upturn.
This auspicious macro-economic environment has had a highly beneficial effect on the employment figures, which in December were running at almost 72,000 people, and were thus 2.7 per cent up on the preceding year. Thus following the low point of 2010, in the wake of the financial and economic crisis they have risen by almost 20 percent.
Germany optimally positioned on the global market
Germany ranks among the world’s leading suppliers of machine tools, a status confirmed yet again in 2017. In terms of production output, German manufacturers are estimated to take 2nd place among the most important producer nations, after China and in front of Japan. “Here, however, the principle involved is ‘class not mass’,” says Heinz-Jürgen Prokop, putting the German vendors’ second placing in its true perspective. China, he explains, produces in many cases low-tech in large quantities for its domestic market, and for developing countries. This is evidenced by the average price for a Chinese NC-controlled machine of 39,000 euros in comparison to 322,000 euros for a German NC machine.
In terms of exports, Germany remained comfortably the export world champion during 2017, in front of Japan and Italy.
In 2018, German manufacturers will exceed the 16-billion-euro mark
For 2018, the prospects are very good. “Firstly, the global economy is growing vigorously, and secondly, international machine tool consumption is predicted to increase by 3.6 per cent,” explains Heinz-Jürgen Prokop. This is primarily attributable to Europe. America is likewise showing vigorous growth, whereas in Asia, by reason of the high growth achieved in 2017, the dynamic is exhibiting a slight weakening.
Finally, last year orders rose by eight per cent. Domestic orders were up by ten per cent, while bookings from abroad increased by seven per cent. It’s interesting, however, to look at the months individually. “Whereas orders decreased during the year’s first half, even by double-figure rates in the domestic market especially, in the year’s second half the logjam disappeared,” says VDW Chairman Heinz-Jürgen Prokop. Domestic orders then soared, with a plus of 41 per cent in October, 67 per cent in November and most recently 37 per cent in December.
All in all, demand for machine tools is more broadly based among the regions than almost ever before. Many companies can benefit from this. The rising level of orders assures a continuation of Germany’s production growth. With a plus of five per cent, it will for the first time exceed the 16-billion-euro mark.
A shortage of specialist staff may torpedo the sector’s future development
Growth is not, however, self-sustaining. A flourishing business cycle and good prospects should not blind us to the fact that the sector is facing numerous challenges. To enable the production forecasts to be achieved, the firms involved will have to mobilise all their capacities. In many cases, though, this will come up against staffing bottlenecks. In certain professions, such as mechatronics engineers or IT specialists, and above all in rural regions, the market for specialist staff has been stripped bare. “The purely numerical bottleneck in terms of specialist staff is, we are now observing, accelerating the progress of automation,” reports Heinz-Jürgen Prokop. Many machine tool vendors are increasingly favouring the idea of an autonomous machine, which performs machining processes more independently of an operator’s availability.
In actual fact, however, the issue is one of staff qualifications. The sector has to cope with the change-over to digitalisation and networking in connection with Industry 4.0, develop new business models and transform its own production operations. Component suppliers in the automotive industry have to develop production systems for new drive trains. Companies that offer and wish to deploy additive manufacturing processes need a new breed of design engineers who are able to translate the advantage of the processes involved into actual products as well. This means that not fewer, but more and differently qualified staff will be required. “The shortage of specialist staff, combined with continued reductions in working hours, as currently being demanded by the trade unions, may conclusively torpedo the sector’s encouraging overall development,” warns Heinz-Jürgen Prokop. At any rate, it may prove impossible for many small and mid-tier companies to compensate for shortfalls due to reduced working hours, sometimes even without any reduction in wages.
Electro-mobility offers opportunities for the machine tool industry
To ensure that the steady upturn of recent years can be maintained, the machine tool industry has to stay on the ball. In particular, for the numerous mid-tier companies, whose biggest customer grouping is the automakers and their component suppliers, and who have tailored their corporate capabilities entirely to these, the change-over to electro-mobility is a major challenge. “Reason enough to analyse possible scenarios with the requisite rigour,” says Heinz-Jürgen Prokop.
The VDMA will shortly be presenting a new, highly detailed study, in which the VDW is also crucially involved. The most important result for the machine tool industry is this: by 2030, the proportion of purely electric-powered cars in Europe, USA and China is predicted to be about a fifth of new registrations. Conversely, 60 per cent of new registrations, with a continuing uptrend, will be hybrid vehicles in different combinations, and the rest, with a continuing downtrend, will be optimised internal combustion engines.
The concomitant decrease in metal-cutting volume is firstly more than offset by the global rise in total registrations for cars, driven by the growing demand in China. Secondly, we are seeing increased complexity of internal combustion technology combined with electric drive concepts.
This entails progressively more stringent requirements for high-precision production technology. Examples include: the reduction of noise emissions in gear manufacturing; higher wear and tear on components entailed when switching over from the electric motor to the internal combustion engine at higher speeds; the more powerful dimensioning of braking systems due to the battery weight; complete-coverage provision of turbochargers. Then there are production systems for manufacturing components for electric drives. These few examples vividly show what production technology will have to be able to offer this segment in future. “For this reason alone, the machine tool will retain its high importance in the manufacturing process of the automotive industry in the future as well, if the transformation to eco-friendlier mobility is to succeed,” is Heinz-Jürgen Prokop’s verdict.
The statement on the opportunities applies for the sector as a whole. The results of the study enable an individual firm to position itself in this scenario and assess its significance for its own product range on the basis of soundly researched data. Machine tool manufacturers who offer good solutions for the above-mentioned requirements can at any rate benefit from this development.
“Once again, it’s obvious that there’s not going to be an abrupt transformation and one single solution for the vehicle drive of the future,” says Heinz-Jürgen Prokop in conclusion. Rather, different drive variants will complement each other. This is particularly true when passenger cars, commercial vehicles and mobile work machines are included. That’s why it’s all the more important for the politicians to drive forward this issue while leaving the technological options open.
Adidas Puma Shoes