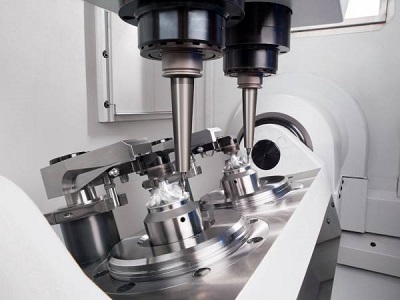
This is also having a positive effect on employment, which amounted to around 72,400 employees (+3.4 percent) at the end of 2017. Production is running almost at full capacity. Dr. Schäfer on the reasons: "The world economy is still growing strongly. According to experts, gross domestic product in 2018 rose even faster than in the previous year. The main driving force is industrial production. This is also affecting international machine tool consumption which increased by 5.9 percent in 2018."
Reference will be made to the keywords of digitalisation, networking or Industry 4.0 on nearly every exhibition stand in Stuttgart. The German Machine Tool Builders' Association (VDW) is also specifically promoting the topic through its industry initiative "Industry 4.0“. The objective of the initiative is to formulate a standard and implement it using software in order to connect different machine control systems to higher-level IT systems by means of a common interface. Renowned machine tool manufacturers, all of whom exhibit at AMB, sat down at a table and set aside their competitive thinking for the benefit of this initiative.
The Heller Group is one of these manufacturers. Klaus Winkler, Chairman of the Board of Management and CEO, said that the reasons why his company was taking part in this hitherto unique collaboration were as follows: "Conventional potential for higher productivity is considered to be almost exhausted. We regard "Industry 4.0" as an approach for making the state of machine tools transparent at all times and evaluating acquired information with already existing data for a purposeful diagnosis.“
Every important control manufacturer is now also involved, thus ensuring widespread use. In particular, this is benefiting small and medium-sized companies whose path to the digital future is being paved. During AMB the VDW will present initial implementations for data exchange with machine tools on its own stand in the Special show "Digital Way" and the associated Congress. All VDW members will be brought up to date during an information event.
Strong upsurge in full processing
In the face of so many bits and bytes, there is a danger that tangible further development of cutting production is being overlooked to some extent. AMB will counter this with a very large number of new and enhanced machines.
Professor Berend Denkena, Head of the Institute for Production Engineering and Machine Tools (IFW) at Hanover University and acting President of the Scientific Society for Production Engineering (WGP), sees signs of a trend towards full processing. "If possible, components should be finished in one machine and from six sides.
For example, grinding technologies are being used to an increasing extent in traditional lathes and milling machines in order to be actually able to produce specific qualities. This is also leading to greater use of zero-point chucking systems if a change of machine cannot be avoided. Too little attention is being paid to the topic of energy efficiency." Denkena regrets that energy is still too cheap. "Especially in the areas of cooling and lubrication, there is untapped reduction potential of up to 50 per cent."
Dr. Oliver Gossel, Sales Director at Röders, a manufacturer of high-speed milling machines, confirms the trend towards multifunction machines. "We are now achieving great success on the market with our machines for milling and grinding processing. The limits of what is feasible are being extended continuously. Examples include surface qualities through to gloss finishing in steel and increasingly higher workpiece accuracies."
New opportunities being opened up by alternative processes
Additive processes are increasingly being integrated as an additional tool in traditional machine tools in order to be able to apply and remove material in one clamping process. As automation becomes more advanced, robots are performing simple machining steps such as deburring in addition to their main handling tasks. All the technologies can meet in the control unit which speaks every necessary language more and more frequently.
Axel Boi, Head of Production Planning in the Chiron Group, even sees additional business through additive processes. "Since, however, mechanical processing of function surfaces is now necessary in all 3D processes, I regard this as more of an opportunity than a risk." Or the machine tool manufacturer Starrag: The increased opportunities of the latest robot generations are already being used. Managing Director Dr. Marcus Otto: "They are not only being used to an increasing extend for automation purposes, but also to perform auxiliary tasks in our projects." Otto added: "Since the field of action of robots is becoming ever larger, we can meaningfully streamline metal cutting in individual cases and offer our customers the necessary increase in efficiency by means of parallel ancillary processes." Other tasks for robots could be different finishing processes, cleaning and testing of workpieces.
No fear of electric mobility
Nascent electric mobility initially led to genuine horror scenarios in the metal cutting industry. Compared with petrol engines, electric engines only consist of a few comparably simple parts. The situation has now eased after a closer analysis. Apart from the fact that experts are still expecting petrol engines to be used for decades, the hybridisation of many vehicles, i.e. fitting with two drive types, calls for even more machined parts. In pure electric vehicles the lower noise level means that the remaining parts must be designed all the more accurately in order to prevent them from becoming annoying. The result: machine tools must be able to produce even narrower tolerances. A clear points victory for manufacturers of high-tech machines.
The automotive industry, the aerospace engineering industry and energy producers are increasingly using new materials either to make components lighter or protect them against increasing strain. The Japanese machine tool manufacturer Yamazaki Mazak is convinced that machining of these parts, whose material removal rates often amount to 90 per cent, necessitates much higher cutting speeds. This depends on perfect interaction between tools and the machine. The torsion-resistant casting frame and high acceleration values of the latest Mazak series ensure "outstanding positioning and machining accuracy" and "highly precise results“.
At the start of last year the machine tool manufacturer Grob, which has a strong presence in the automotive industry, even purchased DMG meccanica, a leading manufacturer of machines and systems for the production of stators for electric engines, alternators and generators. By its own account, Grob has already worked on several electric mobility projects and increased its research and development work on future technologies through the acquisition of DMG meccanica. Grob said that it now has all the main processes and methods for producing electric drives for the automotive industry and its suppliers under one roof and can also supply them worldwide tor series production.
The Chiron Group is also unperturbed. Dr. Markus Flik, Chairman of the Executive Board of the Chiron Group: "In the area of electric mobility special components for new modules and units such as scroll compressors, electromechanical brake servos or electric axle drives are required.
There is also increasing demand for turbochargers and, thus, for compressor wheels made of titanium. Since titanium wears much quicker than aluminium, sister tools must be used here in order to ensure a productive production process. For this purpose, we offer ideal solutions through corresponding machine series and automation systems."
Jordan Hydro 6 Sandals