Recent studies on new materials have led to the development of a new generation of composites with more advanced properties meeting changing requirements of various industries.
Teijin Limited has developed Japan's first prepreg, or carbon fibre sheet pre-impregnated with bismaleimide (BMI) matrix resin that offers high resistance to both heat and impact, making it ideally suited to use in aerospace engine components. Teijin's new BMI resin pre-impregnated prepreg achieves a high glass transition temperature (Tg) of 280℃ and compression after impact (CAI) of 220MPa, a previously difficult combination made possible based on Teijin's original resin-composition formulating technology.
The new prepreg also maintains its coefficient of linear thermal expansion and high dimensional stability at both low and high temperatures. Moreover, by adjusting resin viscosity, Teijin also has improved mouldability by adjusting the resin flow through preforms in the mould cavity and reduced curing time with its new prepreg compared to conventional BMI-based prepregs.
Teijin, having developed technologies to adapt its prepreg for engine components, is now working on other high-heat applications for aerospace. These efforts will be supported with the knowhow and global marketing channels of Renegade Materials Corporation, a provider of highly heat-resistant composites, which Teijin recently decided to acquire.
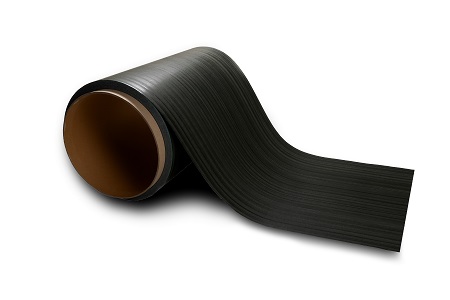
Highly heat and impact resistant carbon fibre prepreg for aerospace applications
Teijin is rapidly expanding its market for next-generation aircrafts by developing midstream-to-downstream lineups and related applications, such as cost-effective carbon fibres with higher-tenacity and higher-tensile modulus and intermediate materials including thermoplastic prepreg.
Prepregs, which are intermediate materials for carbon fibre reinforced plastics (CFRPs), are used in fields ranging from aircraft and automobiles to infrastructure and leisure. As such, their prescribed properties must differ widely depending on the application. To address specific needs, technologies for various combinations of carbon fibre and matrix resin and for specific processing needs continue to be developed.
Prepregs are generally impregnated with lightweight, high-intensity epoxy resin. Conventional BMI resin-impregnated prepreg is already used for high-temperature applications such as aerospace engine components to prevent degradation and deformation. BMI resin, however, loses shock resistance when heat resistance is increased. Also, CFRP made of BMI resin tends to peel apart and crack when subjected to strong impact. In addition, moulding BMI resin can be difficult due to its liquidity.
Multi-material composites
Teijin has also unveiled another achievement of its automotive composites specialty groups which have developed a multi-material composite automotive door concept that maintains required crash specifications while reducing overall weight by 35% when compared to a conventional steel door. A prototype of this unique approach, developed jointly by Teijin Composites Innovation Center (TCIC) and Continental Structural Plastics Holdings Corporation (CSP), was put on display at JEC World 2019.
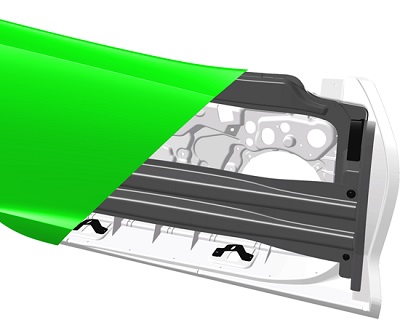
Prototype of multi-material composite automotive side-door module (graphic image)
The module is made from carbon fibre sheet moulded compound (SMC), glass fibre SMC and unidirectional glass fibre reinforced plastics (GFRP) to offer both high strength and low weight. Additional benefits include cost efficiency equal to that of an aluminum door module, and the ability to achieve deep draws and superior design freedom not achievable with a metal. The solution also withstands the heat level of the conventional E-coat automotive painting process.
Tough, lightweight, eco-friendly modules are increasingly being adopted for automotive components such as resin-based tailgates, bonnets (hoods) and roofs to help reduce CO2 emissions and further the range of electrical vehicles. Multi-material side-door modules for high-volume vehicles have been realised by some automakers, however, they still are particularly challenging for designers as these components must meet especially demanding requirements for shock absorption to protect passengers in crashes, fatigue resistance to withstand the stresses of repeated opening and closing and accommodate interior harnesses for electrical wiring and signal components.
Teijin plans to continue enhancing the quality of its side-door module capabilities by applying various high-performance materials and technologies available within the Teijin Group. Leveraging its strengths in composite technologies, the goal is to launch a commercial door module by 2025 and become known as a global supplier of multi-material automotive components, targeting sales worth approximately $2 billion by 2030.
Continental Structural Plastics, a Teijin Group company, has provided leading-edge technologies in lightweight materials and composite solutions for the automotive, heavy truck, HVAC and construction industries for 50 years. Headquartered in Auburn Hills, Michigan, CSP provides full-service engineering support, and holds multiple patents covering materials development and manufacturing processes in composite materials formulation, design and manufacturing technologies. The company has operations on three continents and more than 4,200 employees.
Improving composite properties
Teijin has been taking important steps to advance the properties of composite materials. For instance, its Tenax carbon fibre and carbon fibre thermoplastic unidirectional pre-impregnated tape (TENAX® TPUD) was qualified by Boeing and registered in its qualified products list. This will enable Teijin to supply TENAX TPUD as an intermediate advanced composite material for primary structural parts for Boeing.
TENAX TPUD is a carbon fibre thermoplastic unidirectional pre-impregnated tape made with thermoplastic resin and achieves high heat, impact and fatigue resistances and helps to reduce production costs and improve component manufacturing efficiency thanks to its shortened moulding process. Teijin plans to begin commercial shipments of TENAX TPUD to Boeing approved parts makers in the next two years.
Teijin focuses on the aircraft business as one of the growth strategies in its medium-term management plan for 2017-2019 and is intensively accelerating its development of mid- to downstream applications, such as cost-effective carbon fibres with higher-tenacity and higher-tensile modulus, intermediate materials including TENAX TPUD, carbon fibre thermoplastic consolidated laminate (TENAX TPCL), thermoset prepreg and non-crimp fabric.
In Asia, the company has expanded its base with the establishment of Teijin Carbon Shanghai Co., Ltd. in Shanghai, China and Teijin Carbon Taiwan Inc. in Taipei, Taiwan in 2018 as sales affiliated companies to capitalise on the expanding demand for carbon fibre and further strengthen Teijin’s global business capabilities. Both affiliated companies serve as bases to develop carbon fibre business and expand sales in their promising markets. Previously, offices were established in Shanghai in December 2002 and Taipei in April 2014 to identify demand opportunities and provide customer services in China and Taiwan. These two offices now have been respectively absorbed by the new subsidiaries. Internal collaborations will also be developed with Teijin Carbon Singapore Pte. Ltd., an existing Southeast Asian carbon-fibre affiliated company, to strengthen Teijin’s presence the fast-growing Asian region ranging from upstream to downstream business sectors.
Demands for carbon fibre are growing in China, Taiwan and Southeast Asia. Rising standards of living in these markets are stimulating increased demand for high-end sports and leisure goods made with carbon fibre. In addition, increasing environmental measures and infrastructure upgrades are expected to expand the use of carbon fibre for industrial applications such as wind turbine generators, civil engineering and pressure vessels.
Air Jordan XIII CP3