Industry trends in 2019 point towards heightened role of Asia in the global plastics industry. The region, known for having the fastest-growing sectors dependent on plastics, has taken more aggressive steps to show the world that it is still the market to watch with more potential for growth. The World Bank raised its forecast for East Asia and Pacific (EAP) region at 6.1% in 2019, faster than the projected world economic growth of 3%. In particular, the economic expansion in Southeast Asian countries will remain robust: Indonesia to grow by 5.3% in 2019; Thailand by 3.8% ; Philippines by 6.7%; Malaysia by 5%; and Vietnam by 6.6%.
Increased investment inflows into the region is pushing industrial activities, especially in sectors dependent on plastics and rubber. The Southeast Asian plastics market is expected to post about 5.5% annual growth up to 2023 with construction, automotive and packaging being the dominant applications for plastics in the region. In general, the Asia Pacific region continues to play a key role in the global engineering plastics market with growth projected at over 8% annually until 2026, fuelled by increased demand for lightweight automobiles and value-added packaging. As Asian businesses move forward in adopting the Industry 4.0 concept, advanced technologies, production processes and raw materials will be in high demand to achieve digitalisation, IoT and further automation.
International Plastics News for Asia gathered the insights of leading industry players on emerging trends and factors that could affect their operations, the products they will highlight and plans for 2019.
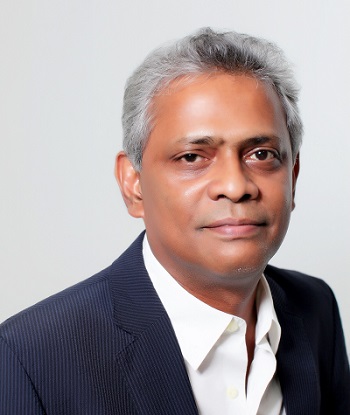
Mr. Sekaran Murugaiah
Vice President, Business Development, Asia-Pacific
Davis-Standard LLC
Website: www.davis-standard.com
"The flexible packaging segment continues with significant growth in the region and will remain a core market we will serve in 2019. We are committed to supporting the medical and automotive segments where Davis-Standard supplies profile and tubing solutions. Key account management processes will be further enhanced in the region.
Our subsidiary in Suzhou continues to be central to our growth in Asia with developments in the areas of machine building and assembly inventory and aftermarket services, field service engineering and installation at customer sites. We will be supplying a 300-metre-per-minute extrusion coating and lamination line for the flexible packaging convertors in 2019.
Challenges anticipated for 2019 include economic uncertainties on the part of investors caused by the US/China tariff war. This has resulted in increased input costs, weakening regional currency exchange rates against the US dollar and potential increases in US interest rates. Additionally, there is a perception of a global recession setting in 2019/2020. Davis-Standard has faced similar challenges in the past and we are confident in overriding these challenges. We will also be geographically focusing on less risky markets and businesses.
The Davis-Standard dsX flex-pack™ 300S is an exciting new product for 2019. It is an extrusion coating and lamination line for the flexible packaging segment developed to meet both the technical specifications and price point for Asian customers. Additionally, Davis-Standard’s presence and regional infrastructure will be an area of focus with the company’s recent acquisition of Brampton Engineering in 2018. Davis-Standard has a significant installed base in the Asia-Pacific region, and we see a key vertical opportunity in the aftermarket, upgrades and optimisation of lines for performance. Specific markets Davis-Standard will be focusing on include China, India, Korea, Taiwan and the growing ASEAN markets."
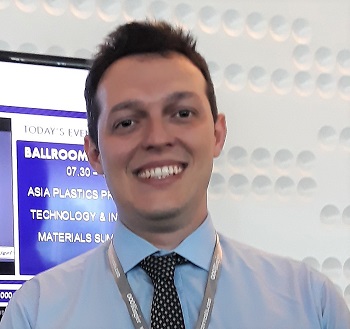
Mr. Claudio Domasi
Sales Director
Frigel Asia Pacific Co., Ltd.
Website: www.frigel.com
"All of the industrial equipment sector is facing a revolution in terms of control and communications systems in response to the trend towards Industry 4.0. The Asia Pacific is coming after Europe in this revolution but the trend is starting as we already see the interest of top level companies in these technologies. The Frigel product portfolio is already completely Industry 4.0 ready in terms of hardware; however the software integration is a continuous development that will be carried ahead in 2019 and afterwards. With the European chiller production facing tough competition due to the more stringent regulations and higher costs of refrigerant gas in the European Union compared to the other countries. Frigel Asia Pacific will start the production of Industry 4.0-compliant Microgel chiller units for the injection moulding in Thailand in 2019, making our company the first one producing dedicated chiller units for injection moulding in Asia Pacific.
In terms of factors that will impact the industry, the trade war between US and China may bring several consequences for the operations in Asia. The Frigel group is already expanding the local presence in each territory with local offices and production sites in order to overcome this situation and boost the commitment in supporting our customers everywhere in the World.
For 2019, the Frigel Group is completing the integration with Greenbox which will bring the Mould Dehumidifiers, Heat and Cool temperature controllers and the unique Capcooler unit in the Group's product range. Also the small Air Cooled chillers and central Water Cooled chillers ranges will be revised as part of this products integration. The year 2019 will also see the launch of the newest version of the Frigel key product in the plastics industry which is the new third generation of the Microgel chiller. The new Microgel range will be made of more than 1,000 different versions in order to adapt to all the requirements of the plastic market."
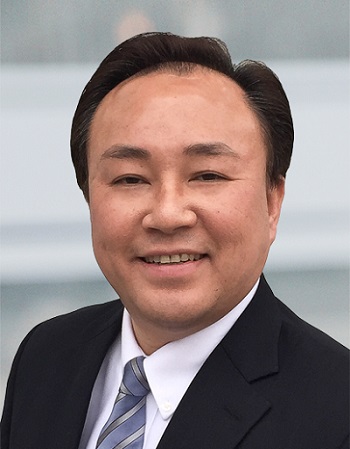
Mr. Geoffrey Chan
CEO
Shunde Kautex Plastics Technology Co.,Ltd.
Website: www.kautex-group.com
"Consumer packaging is one application area that has shown consistently growing demand over the last few years. In this year’s international trade shows such as Chinaplas and NPE, Kautex noted renewed interest from the visitors, whereby the focus was predominantly on the packaging industry. Packaging machine is one of our core businesses and the Kautex Group intends to strengthen our advantages of high quality as well as reliability in this field. In this area, Kautex packaging machines such as the KCC blow moulding machines and KBB all-electric machines are taking the lead.
Digitalisation is radically changing the processes and procedures in every area of work. Companies that do not have a digital strategy will quickly lose their connections. However, digital transformation also means that customer experiences can be optimised to create additional value for customers.
Kautex takes the initiative to meet these new requirements and opportunities as a result of the trend towards digitalisation. In Kautex new machine and service business, there are many advantages to digital transformation for our customers. These include such aspects as training people, and testing parameters and products using purely virtual machines. At our headquarter, Kautex development engineers are examining technical options for the ability to order replacement parts directly from the machine.
Kautex is also working on additional digital applications such as predictive maintenance and augmented reality, by which will contribute to minimise machine idle time or down time and providing strong sales support."
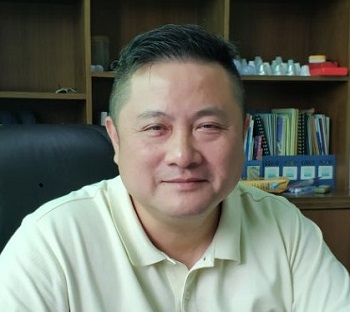
Mr. Percy Yu
Overseas Sales Department
Fomtec Plastic Machinery (Guangzhou) CO.,LTD.
Website:www.fomtec-group.com
"Fully automated production is a perennially important subject in plastic processing. In this area, Fomtec has accumulated over 30 years cooperating with other parties to assist end-users optimise their production processes. Fomtec vertical injection moulding machines had many successful cases integrating robot arm, mould and auxiliary equipment to produce multi-colour/multi-material products through full automation.
For 2019, the demand for efficient production systems continues to impact on how Fomtec operates and we believe that our machines can do more to fulfill our customers’ requirements. Our Turret type Multi-colour/Multi-material model is under client’s mission to run in their plant room. This machine design enables the customer to save on costs. For certain products, the vertical injection moulding machine with robotic arm combination is the only choice. One vertical machine model for one-colour must need to link up four machines with robotic arm to produce 4-colour toys, for instance. Fomtec also offers thermoplastic+thermosetting machine in which material selection and coordination are the most important factors to consider.
Under the unpredictable world trade situation, we must keep a positive mind and step forward. Fomtec will continue to assist customers through our Asian sales agents before and after sales."
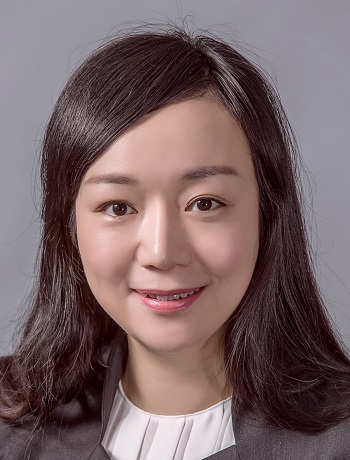
Ms. Ina Jiang
Vice President of Marketing
FRX Polymers
Website: www.frxpolymers.com
"The International Monetary Fund on October 9, 2018 cut its global economic growth forecasts for 2018 and 2019, indicating that the US-China trade war would take a toll and that emerging markets would struggle with tighter liquidity and capital outflows. FRX Polymers is monitoring this development carefully as it will surely impact the Chinese market. FRX believes that the ultimate impact of this trade war on its operation can be neutralised by virtue of FRX’s well positioned state-of-the-art production facility in Antwerp, Belgium. In this way, FRX Polymers will be in a position to continue to provide world-class quality products and services with a competitive cost position.
We are very excited that our groundbreaking innovations in FR films and fibres, PUR foam, and printed circuit boards are gaining strong market traction. In FR Polyester fibre, Nofia® halogen-free flame retardants enable our clients to: 1) expand their product offering with phosphorus content from 3,000 – 22,000ppm which is not possible with the incumbent FR technology; 2) use high-recycle content while maintaining strong FR and mechanical performance; and 3) use various feedstocks for the production of FR fibres. Moreover, Nofia-based FR polyester fibres have higher tenacity which results in up to 35% faster fibre spinning speeds and also allows our customers to enter the high-tenacity FR fibre market.
Several factors are expected to impact the plastics industry. Demographic shifts will require better protections for an ageing population and consumers have a very different expectation of safety than previous generations. Governments are also driving regulations on environment protection and consumer safety. As the world’s only polymeric halogen-free flame-retardant additive, Nofia® Polyphosphate products deliver outstanding fire safety while simultaneously providing a green sustainable solution.
A total of 3.5 million tonnes of waste are produced around the world every day and this figure is predicted to almost double by 2025. The goal of the circular economy is to reintroduce products at the end of their life cycles into new useful products. However, recycled materials often have inferior properties compared to virgin materials. Nofia® halogen-free flame retardants have been proven to deliver improved mechanical and FR properties for PET fibres produced from recycled stream of PET bottles. In the area of 5G or fifth-generation cellular wireless, Nofia® halogen-free flame retardants have been proven to reduce transmission loss and improve product reliability in printed circuit boards for electronics and high-speed servers which positions FRX Polymers well for the coming 5G revolution. In addition, for the automotive markets, from 2019 onwards, various countries will launch new regulations related to improving vehicle air quality standards by mandating the reduction of volatile organic compounds (VOC) emanating from plastics used in the passenger compartment. Nofia® polymeric halogen-free flame-retardant products replace the small molecule volatile flame retardants in polyurethane foam in headliners which has allowed our customers to meet stringent reduction in VOC, including the new Chinese national standard GB/T 27630-201X and Germany’s VDA 277 and 278."
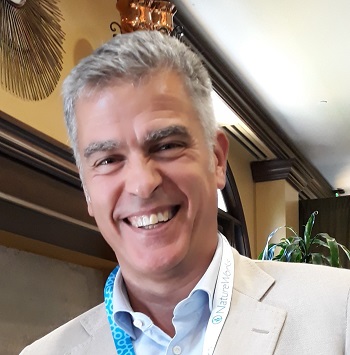
Mr. Marco Garilli
Innovation Expert - Polymers
Global Connectivity & Technology, Global Operations
Electrolux Italia SpA
Website: www.electrolux.com
"A real step change in the household appliances sector is the application of bio-based plastics, which have been well known for their application in disposable products, but are also gaining acceptance in consumer durables despite some limitations. New opportunities and possibilities are opening up in the use of bio-based materials in the household goods sector in response to the growing focus on sustainability. In particular, the use of PLA in place of PS to produce a real prototype of a refrigerator by using two different technologies, such as extrusion/thermoforming and injection moulding, is a clear evidence that everything is now ready for a real step change. Even though there is some development work to do before reaching the stage of commercial production, this is a great opportunity to take into consideration. The application of biomaterials to products like appliances, produced in tens of millions per year, is therefore extremely significant and can really lead to a strong reduction in CO2 emission worldwide.
Electrolux has been continuously evaluating new opportunities for the company to introduce sustainable materials, including recycled materials through various research activities. Our collaboration with our partners, such as NatureWorks for the materials, has enabled us to select the right sector to demonstrate our innovations and, for consumer appliances, the refrigerators have been selected. For the household appliances sector, the future could see an evolution to find an alternative to ABS. Electrolux has strict requirements on ABS, especially as far as light resistance is concerned. PLA, properly formulated, could provide a significant improvement in this direction.
The Asian market is growing and in some cases, finding replacement in Asia can be an alternative. Electrolux needs to cope with difference markets with diverse specifications for appliances."
Jordan Flight Luxe