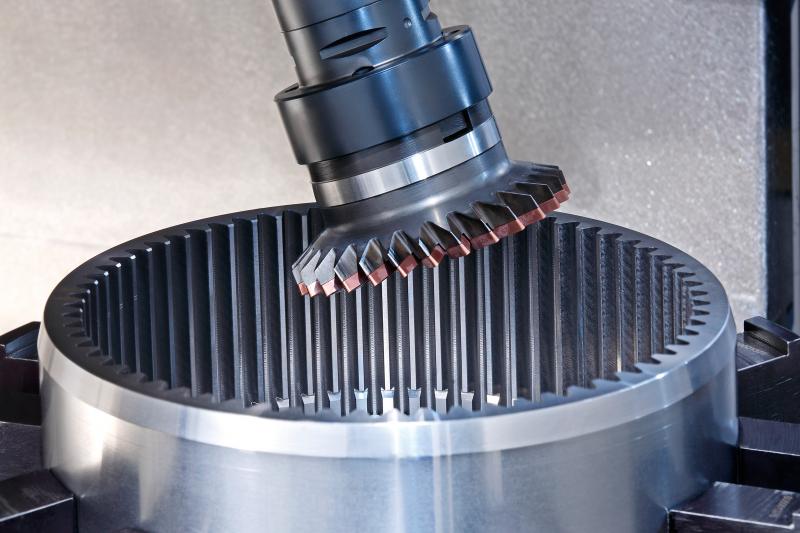
Intelligent tooling concept
PITTLER T&S is facing these complex customer requirements related to the production of components for commercial vehicles with complete machining solutions which combine various manufacturing technologies, tailor-made automation concepts and high-precision measuring and tooling engineering. The latest result of the innovative strength of the Dietzenbach-based DVS company: the PITTLER SkiveLine machine series, a modular Power Skiving gearing center including complete machining, automated loading and unloading as well as an intelligent tool and measuring concept for highly efficient series production.
The successful PV machine series from PITTLER T&S GmbH was specially designed to meet the formidable requirements in the field of commercial vehicle component production and is particularly suitable for a large range of gearbox components such as planetary and hollow wheels. As a pioneering further development of the PV series, the turning and gearing specialist within the DVS TECHNOLOGY GROUP is extending its product portfolio by the innovative PITTLER SkiveLine series, an innovative high-performance gearing center. This way, PITTLER T&S is continuing to expand its leading market position as the only supplier of Power Skiving gearing solutions including complete machining for the precise and economical series production of rotation-symmetrical components. With the introduction of the new machine series and thanks to extraordinary progress in the field of technology development, the DVS company from Dietzenbach in southern Hesse/Germany is now able to offer Power Skiving not only exclusively as a soft machining process but also as a hard-fine machining process – i.e. Hard Skiving – for the first time.
Engineering of Power Skiving tools from a single source
In order to produce internal and external gearings using the highly productive Power Skiving method, with modules greater than 3 – in contrast to a pure gearing machine – a skiving tool for rough skiving and then a finishing skiving tool are exchanged in the work chamber via the tool magazine of the 5-axis gearing center. Thanks to this procedure, during which the rough skiving tool removes more than 80% of the necessary machining volume, the process goes easy on the higher-quality finishing skiving tool, thus increasing the latter’s service life. Due to the significantly higher cutting speed during rough skiving, the process time for gearing production is considerably reduced despite the necessary tool change. Depending on the concrete application case, finishing is carried out by cylindrical or tapered powder-metal-coated tools which can be decoated, sharpened and coated again after the end of their service life. For maximum customer benefit, the DVS company provides the entire Power Skiving tool service from a single source, from requirement-specific production to repeated tool treatment.
Internal and external gearing with complete machining in a single clamping
This is a major factor in optimally playing out the advantages offered by the Power Skiving technology continually developed by PITTLER T&S and culminating in the new PITTLER SkiveLine series rather than conventional gearing technology such as broaching, hobbing and gear shaping, since it can produce both internal and external gearing up to quality class IT5. On the tooth flanks, users meet highest surface requirements with an Rz value of less than 3 µm, while at the same time achieving a machining time reduced by a factor of between three and eight compared with competitors’ methods. Thanks to the integrated tool magazine which offers room for more than 20 different machining tools, users of the PITTLER SkiveLine can implement upstream and downstream working steps such as turning, milling, drilling, deburring and measuring in addition to the Power Skiving process with great precision and reliability in one work chamber and one single clamping. Tool changing at the multi-function head always takes place parallel to the machining time and permits flexible adaptation of individual procedures of the complete machining process. Precision-reducing reclamping errors as well as non-productive set-up, transport and holding times required by conventional lines with several individual process machines are thus a thing of the past. This also allows manufacturers to react economically to varying batch sizes, which is not possible with sequential production. In addition, the tool magazine in the skiving center allows optimized sister tool management, which makes a significant contribution to a more productive series manufacturing design. In order to guarantee reliable cooling and controlled chip removal, PITTLER T&S uses emulsions, compressed air or a combination of both, depending on customer wishes and requirements.
PITTLER Automation Cell for highly efficient series production
The new PITTLER SkiveLine has the specially developed PITTLER Automation Cell available, PITTLER PAC for short, particularly with the further expansion of the performance spectrum in mind with regard to the fully automated series production of rotation-symmetrical commercial vehicle components. Components with a diameter of up to 270 mm, a maximum height of 150 mm and weighing no more than 16 kg are loaded and unloaded into and out of up to two work chambers via an integrated workpiece shuttle system and short travel paths, thus reducing workpiece changeover time to less than five seconds – an outstanding value which cannot be achieved using the pick-up technology usually available on the market. The almost complete separation of loading and unloading paths inside and outside the work chamber also effectively prevents cooling lubricants and chips being carried over. The standard version of the extremely compact PITTLER PAC with a footprint of just 4.5 m2 includes both an SPC discharge and an NOK belt, and can be expanded further by additional testing and machining systems thanks to the cell’s modular design. In order to check the quality of machined gearings quickly and easily, a twin-flank testing device can be integrated, for example, the measuring results of which the machine can use continually for specific correction and readjustment – in order to guarantee the maximum production quality of each and every workpiece. Building on its vast range of relevant expertise, PITTLER T&S offers customized, application-specific automation solutions e.g. in the form of robot-supported manufacturing cells or pivoting grippers with connected conveyor belt integrated into the work chamber for components which exceed the dimensions specified above.
Another innovative functionality of the new machine series that has a positive impact on the more efficient production design is the user-friendly skiving interface, which guarantees users fast and reliable control and monitoring of the Power Skiving gearing centre. Depending on the geometry and process data required, the control software independently calculates the adequate machining program and initiates the manufacturing process at the push of a button. Important parameters such as for the two-ball dimension and quality of the flank line can be determined and evaluated directly for a constant quality check. Specific corrections of the profile and flank line angle are also possible directly.
There are different machine types of the new Power Skiving gearing centre from PITLER T&S GmbH available for commercial vehicle components of different diameters: P-SK 400 (up to Ø 400 mm), P-SK 630 (up to Ø 630 mm) as well as P-SK 1250 (up to Ø 1250 mm).
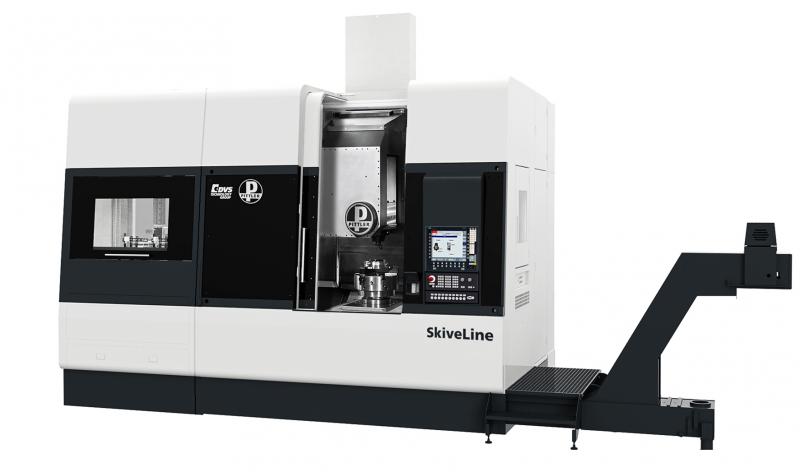
PITTLER SkiveLine
Nike Schuhe