The electrification of cars is transforming the automotive industry and Polyplastics Co., Ltd. is responding with innovative resin products which are successfully penetrating the electric vehicle (EV) market as a superior alternative to metals. The company’s DURANEX® PBT and DURAFIDE® PPS materials - targeted for engine peripheral parts such power control units (PCUs) – deliver high insulating properties, lower water absorption, and meet harsh operating conditions (-40°C to 150°C, up to 95% relative humidity).
Polyplastics’ DURANEX® PBT CG7030 provides lower water absorption and high tracking properties (CTI: 600V) for high-voltage parts such as PCUs. The material ensures high reliability for high-voltage parts that do not gain enough creepage distance. Water and salt can penetrate high-voltage parts and cause tracking issues so materials with high CTI values are required.
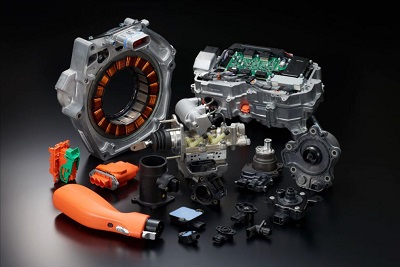
Polyplastics also offers DURAFIDE® PPS 6150T73, which provides high heat shock resistance, strong dimensional stability, and excellent heat and chemical resistance for metal insert molded applications for electric vehicles. Previous material technologies suffered from lower heat shock resistance when moldability (flowability) increased.
Polyplastics is also exploring new materials to replace metal in PCU housings. Thermoplastics would provide lighter weight and improved productivity, however, other key requirements include strength, dimensional stability, electromagnetic shielding, and thermal conductivity. Specifically, Polyplastics is currently developing materials with electromagnetic shielding properties. The company is also targeting its material development work for other EV applications such as motors and batteries.