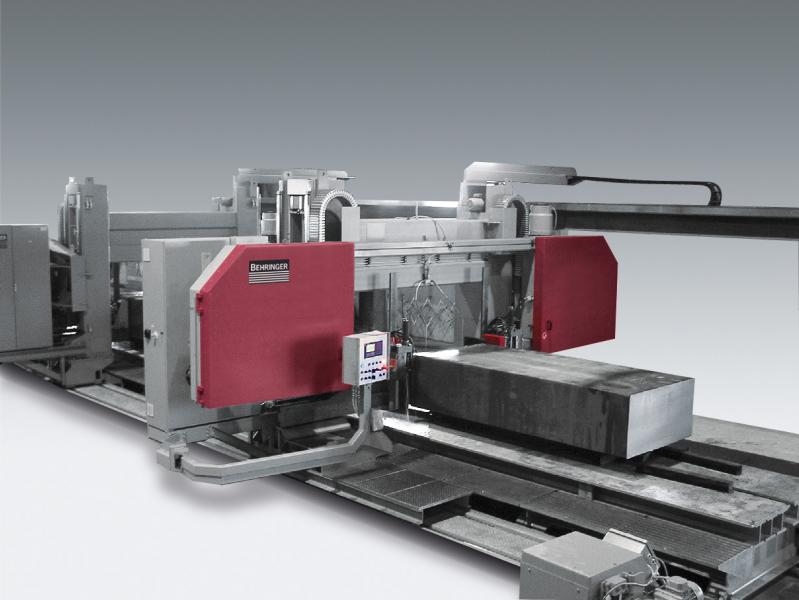
The everyday world of work encountered in forges, steel works and other industries faced with similarly tough working conditions makes heavy demands on the durability of machine tools. As well as being resistant to dirt and dust, they are also required to withstand extremely heavy weights while continuing to work with the utmost precision and reliability. The large-scale bandsawing machine HBP1100-1500 Gantry has been designed specifically to meet these demands and is also available with several sawing units working in sequence. In forges, rolling mills and gravity die casting foundries, and also for steel finishing applications, this machine is a specialist in cutting rods, notching material samples and sawing usable parts. It is ideal for cutting large workpieces such as ships’ crankshafts, turbine shafts, metal blocks or large-scale tools.
The high level of cutting accuracy and long saw blade service life are due to the special dual-column design and the use of vibration-damping grey cast iron to make all the blade guiding elements. The machines are fitted with a sawing frame mounted on two grey cast iron columns, which traverses over the workpiece. Working hand in hand with the completely backlash-free, wear-free pre-tensioned guides, this dual column concept creates an optimum vibration damping effect and guarantees extreme cutting precision.
On each side of the saw frame, side elements have been arranged using pre-tensioned linear guides. These accommodate the band wheels and guides. The sawing gantry is mounted on a system of four rails equipped with a frequency controlled traversing drive. Traversing and positioning take place using a manual inching mode. During the cutting process, the gantry is electromechanically clamped to the rails. Saw blade drive takes place using a frequency controller located in the switch cabinet. The cutting speed can be adjusted and read at the control desk. A servo drive with two ball screws and an electrically coupled gear ensure consistent movement even at very low saw feed rates. The feed control facility, which comes as standard, and cutting force absorption directly at the saw blade help to maximize the saw blade life. As a result, high cutting outputs and an economical saw blade service life are no longer mutually exclusive. The machine can optionally be operated with a constant cutting feed rate or constant cutting pressure. This provides the guarantee of precise cut sections and optimum bandsaw blade capacity utilization. The feed rate and cutting pressure are set steplessly at the terminal, which displays the actual speed in digital form. Motorized double brushes arranged on both sides ensure optimum gentle-action cleaning of the bandsaw blade. The brushes are fed towards the blade automatically.
Clamping and gripping in safety
The solid support table is permanently anchored to the hall floor. The sawing units are manually positioned for cutting by means of frequency-controlled drives.
Because a durable clamping device is indispensable when it comes to the economical sawing of workpieces such as slabs with scaled surfaces, the gantry variant is fitted with a centric material clamping facility in which the two vices and guide arms can be fed independently of each other. The material weighing several tons is clamped into its initial position on the table without needing to be moved. The material support table also comes with a highly functional, durable design for tough application conditions. The supports can be variably adjusted in line with the material being sawn. For round material, for instance, prismatic supports are offered, for flat material flat supports with a stop.
The HBP1100-1500 Gantry also has some outstanding features to offer when it comes to the sawing process itself. To saw materials with difficult machining properties, up to 15 kW of output power and special high-torque gear speeds are available. To allow samples to be notched out of the material, cuts can also be performed in the horizontal direction, as the bandsaw blade guides are configured to permit 90° rotation. This entails positioning the sawing frame to the required cutting height. During horizontal sawing, the sawing frame’s servo drive powers the saw feed by means of an electric motor.