
Shotblast resistant marking before after laserax
Laserax will launch its exclusive patent-pending shot blast resistant laser marking process at the 2018 Die Casting Congress & Exposition, which will take place from October 15 to 17 in Indianapolis, IN.
For the past three years, laser experts at Laserax have been working to provide die casters with foolproof traceability systems that are able to mark permanent identifiers directly on the castings. A breakthrough was achieved with the help of our development partners at Cascade Die Casting Group and Mercury Marine.
With Laserax’s patent-pending laser marking process, it is now possible to identify parts right out of the die and feature tracking codes that will resist any post-process treatments, including shot blasting.
HAVING PARTS MARKED RIGHT OUT OF THE DIE: THE NEW REQUIREMENT
Ever-increasing requirements by automotive manufacturers are pushing die casters towards a perfect traceability system from the extraction of the casting from the die through to any post-process treatment and all the way to automotive assembly lines.
“The whole challenge was to find a partner with the same can-do attitude and hardworking mindset that are at the heart of Cascades Die Casting Group’s culture. We found in Laserax exactly what we were looking for. And, together, we made the impossible—possible,” said Mark Petro, Director of Engineering at Cascade Die Casting Group.
“At Mercury Marine, having parts with shot blast resistant markings meant being able to track critical parts individually throughout the supply chain. Mercury Marine continues to set the standard for extreme reliability and intuitive operation of marine propulsion systems. Laserax has been a great partner in improving the traceability throughout our manufacturing operation,” explained Alex Monroe, Engineering Project Manager at Mercury Marine.
COMMITTED TO SOLVING CUSTOMER TRACEABILITY CHALLENGES
“Maintaining the legibility of a part identifier through shot blasting was no small feat. It involved testing several parameters. Many iterations were required. Many hypotheses were formulated and rejected based on the test results. But in the end, our commitment, expertise and creativity prevailed,” explained Alex Fraser, CTO of Laserax.
“The development of shot blast resistant markings is a great example of what we are and what our teams do on a daily basis: working with great partners such as Mercury Marine and Cascade Die Casting Group to push limits of lasers forward through the most demanding industrial applications,” said Xavier P. Godmaire, President of Laserax.
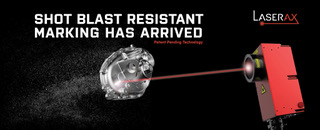
Shotblast resistant marking
About Laserax:
Laserax is a laser system manufacturer that provides effective, reliable and safe solutions for the most demanding industrial applications. We rely on a team of laser technology experts to offer a complete range of products for laser marking and laser cleaning.
Off White X Nike Design