A Sweden-based recycler is known for being a professional recycler that also collects plastics from waste electrical and electronic equipment (WEEE) and other products from the automotive sector such as bumpers, battery packs, engine piping, etc. These post-consumer waste contains iron particles, wood pieces and paper labels, etc. Thus, a turnkey solution starting from material sorting, cleaning, drying and processing into high-end quality recycled pellets are essential factors toward business success. Thanks to the simplest yet powerful design of POLYSTAR’s recycling machine, integrated with FIMIC’s advanced auto cleaning filtration system that ensures excellent filtration efficiency and continuously high output performance.
The collected post-consumer ABS and PS regrinds have higher bulk density of 200-600 kg/m3 and moisture. Thus, washing and sorting processes should function well so that the sorted recycled material will be in cleaner form. POLYSTAR customizes the tailor-made screw profile design which is optimized the melting flow paths and activities for both materials, and the specific pelletizing die head design is also beneficial for stabilizing the quality and consistency of the pelletizing process. Moreover, the customer requested the intelligent water level sensing control on the vibration tank to optimize the cooling efficiency in time. With POLYSTAR simplified and user-friendly structure design, the cooling temperature can be visibly monitored and controlled via intelligent PLC control system, and the average output of the Repro Direct 150 is able to reach up to 700~800 kg/hr for the business benefit of the Sweden-based customer.
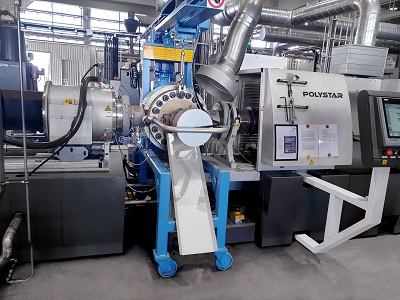
As a professional recycler in the post consumer recycling industry, the excellent quality of the recycled pellets and high efficiency of machinery operation are the most important two indicators that the POLYSTAR customer pursues. Hence, it considers that the simplest yet powerful machine of POLYSTAR, and its high degree of fully automation control system can meet the reycler's expectation. By adopting with SIEMENS state of art PLC plus POLYSTAR intelligent HMI touch panel control system, the energy and current consumption can be monitored in-time, and the feeding, cutter compacting, extrusion, filtration, pelletizing units are flexible switched control and data setting precisely. The other value-added functionality of this smart PLC control system includes: preheating sequence of the extruder temperature for higher degree of automation; process parameter data setting ,recording and simulation; operation data curve analysis; and operation error alarm and in-time report.
For processing the post consumer grade waste material, the efficiency of filtration system should be the critical factors for the higher quality and stable throughput. After comparison of several advanced melt filter solution by the customer itself, they finally choose Italian FIMIC auto-cleaning filtration system as the higher cost effective solution. Thanks to the similar “ Simple yet Powerful” design concept and mentality of FIMIC, the FIMIC filter can be perfectly integrated with POLYSTAR recycling line to perform the best filtration capability via mutual technical cooperation.
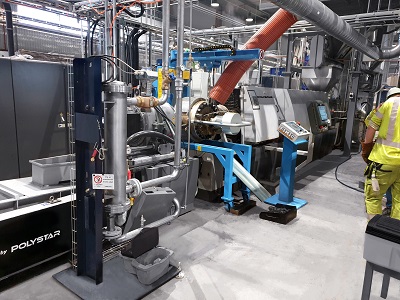
After converting the home appliance waste into recycled pellets, Degree of degradation is the major concern. Thus, the customer put back the recycled pellets into the injection molding machine for production and verify the impact resistance, tensile strength and flexural strength of the end product. As a result, the quality is met with our criteria and expectation, POLYSTAR proven its merits not only at its machinery, but also with the excellent quality of recycled pellets. A proportion of the recycled pellets will be mixed with the confidential additives and powder formulation into compounding process and develop the reinforced material for high-value market.
For more information: /www.polystarco.com/en/index.html