Proco Machinery Inc. has launched a unique lay-flat packing technology which allows blow molders to pack plastic bottles on their sides, as opposed to placing them with necks up or down. The new tooling technology makes innovative use of collaborative robot automation systems from Universal Robots, based in Boston, Mass.
Proco Machinery is working closely with Universal Robots to offer a complete downstream automation solution for the blow molding industry, according to Siva Krish, vice president of sales for Proco Machinery.
Proco’s new Lay Flat Tooling innovation helps blow molders and brand owners maximize product capacity for a given container. The company has developed two sets of tooling for two different applications - one for straight neck-to-neck packaging in the box and another for offset neck orientation from row to row. This potentially allows a blow molder of bottles to pack 270 bottles in a box instead of 250, resulting in maximized capacity and tremendous savings on freight cost.
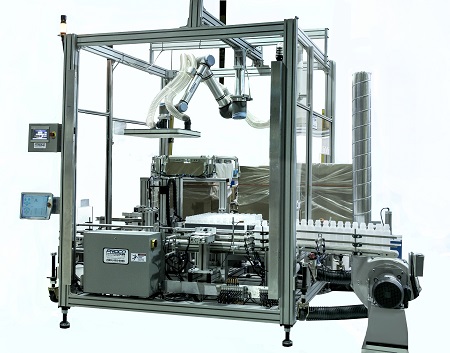
For Proco’s unique lay-flat system, the company designed a solution to counter the cobot’s inherent desire to resist force. “You need to have a small bit of clearance between the box and bottle so the tooling arm goes in and comes out,” Krish explained. Ultimately, the design of the bottle determines how Proco customizes the robot’s packing routine. “Every bottle and every pack count and every production line will be completely different,” he said.
The lay-flat technology gives blow molders more flexibility and widens the scope of containers that can be packed automatically. The bottom line is that blow molders and brand owners can benefit from an attractive return on investment (ROI) when incorporating Proco’s innovative lay-flat tooling technology.
Proco Machinery has developed several different options for packing bottles inside a box including a patent pending End-of-Arm Tooling specifically designed for PET bottle applications.
Proco is incorporating collaborative robotic automation systems in a range of products including its collaborative robotic Half-Cube Palletizer system and the Robo Packer case packer. Both new products are attracting broad interest in the packaging market due to the need for greater efficiency and automation. These systems are being designed in such a way that they complement the production line and provide simplified operation, a smaller footprint, reduced bottle handling, and enhanced efficiencies.
Nike Shoes