The WACKER Group officially brought a plant for manufacturing pyrogenic silica on stream at its US site in Charleston, Tennessee. Representatives from the government and from business attended the ceremony. The facility has an annual production capacity of 13,000 metric tons. WACKER will use this output both for sales purposes and for its own silicone production. Highly dispersible pyrogenic silica is an important formulation component for manufacturing silicone rubber. Investments for the new facility total around US$150 million and lead to 50 new jobs at the Charleston site.
Up to now, WACKER has produced pyrogenic silica at its German sites in Burghausen and Nünchritz and at its Zhangjiagang site in China. Launching the new plant in Charleston now puts the company in a position to offer customers in the Americas a direct supply of HDK® pyrogenic silica. “The additional capacity will strengthen our market position as one of the world’s leading pyrogenic silica manufacturers and will help us meet our customers’ growing demand”, as WACKER CEO Rudolf Staudigl explains.
The new plant also closes material loops and improves the supply chain at the site. WACKER has been producing polysilicon in Charleston since 2016. The most important by-product of polysilicon manufacturing is tetrachlorosilane. This material can be either converted and fed back into the production loop or can be processed into pyrogenic silica, thus creating additional value for the company and for customers.
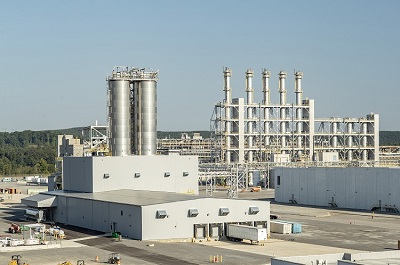
The facility is another milestone for Charleston, as the site is now able to run an integrated production based on the closed loop system WACKER successfully operates at its Burghausen and Nünchritz sites. The network maximizes the site’s flexibility for processing tetrachlorosilane and obviates the disposal of waste products, thus enhancing the viability of the integrated production network as a whole. “The pyrogenic silica facility is the next logical step in making Charleston a fully integrated silicon site in the world’s second largest chemical market,” says Staudigl, emphasizing the strategy behind the investment.
In addition to state-of-the-art dispensing and packaging systems, the new plant will also include test and development labs as well as training rooms for the company’s WACKER ACADEMY. Here, customers can participate in seminars, training sessions and hands-on exercises for an in-depth look at the wide array of applications when using pyrogenic silica. “The inclusion of laboratories supports customers throughout the Americas region with formulation refine-ments and new applications development. Our aim is to further enhance our customers’ product performance,” said David Wilhoit, President and CEO of Wacker Chemical Corporation, during the ribbon cutting ceremony.
WACKER is one of the leading manufacturers of pyrogenic silica (brand name HDK®). This exceptionally versatile powder is produced at the company’s Burghausen and Nünchritz sites in Germany, at the Zhangjiagang site in China, and, as from today, in Charleston, Tennessee, USA, too. Pyrogenic silica consists of highly pure amorphous silicon dioxide. The powder is used as a reinforcing agent in silicone elastomer manufacturing, as a flow-control additive in paints, adhesives, unsaturated polyester resins and plastisols, and as an anti-caking agent in the cosmetics, pharmaceutical and food-processing industries.
Vapormax