The biennial exhibition TaipeiPLAS brought more value-added features in this year’s edition. For one, the ShoeTech Taipei was held concurrently for the first time. A total of 533 exhibitors occupying 2,738 booths presented the collective strength of the supply chain enriched with the existence of comprehensive upstream, mid- to downstream manufacturers in the plastics and footwear making sector.
Getting smart in a greener way
TaipeiPLAS this year focused on one aspect that recent technologies have been aiming for and that is to be eco-friendly aside from being smart. A number of manufacturers have refined their machinery with energy-saving features as defined by carbon reduction, clean operation and limited noise. In addition, the IoT technology, which is supposed to highlight the benefits of data transparency and instant interaction, is being assessed even further in the plastics manufacturing sector for its practicality. The result is the introduction of better injection quality with real-time melt-temperature sensing and process control, and monitoring systems that supervise process optimisation, position sensing, and energy monitoring. Even the need for maintenance will be reduced if the anomalies could be detected during production in time, and the lifespan of components identified beforehand. These all point to a stronger and more sustainable condition for machineries with smart features. These applications are showcased in five major themes at TaipeiPLAS – including the autoparts, medical equipment, packaging, construction materials and tablets.
One of the most anticipated event at TaipeiPLAS 2018 was the summit – themed as “Shaping New Plasbility”. Speakers from top international suppliers including ENGEL, Arburg, Wittmann Battenfeld, and well-known local manufacturers in Taiwan such as FCS, Diing Kuen, HIWIN contributed to topics of digital transformation, injection moulding machines combining key components for automation, SMB applications, and production efficiency.
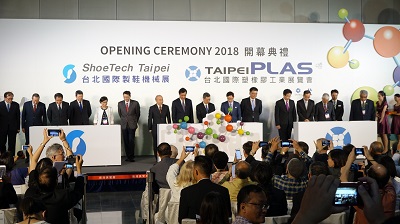
Exhibitors feedback
CLF exhibited 230AE full-electrical injection moulding machines and smart injection moulding machines with automation cell CLF-60TX. Dennis Du, the R&D Manager explained that 230AE saves 5-10% energy consumption and its clean processing receives great interests from buyers from the electronics and food sector. “The biggest highlight of 230AE is its demonstration of folded cap production. We have integrated the folding procedure into our injection machine, which makes greater speed and also space efficiency”.
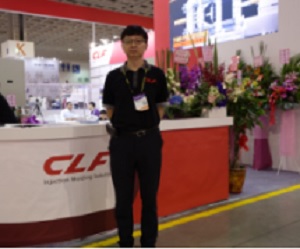
Mr. Dennis Du, R&D Manager of CLF
Shine Well General manager Long Guo Ren explained how the company’s Toggle Energy Saving Injection Moulding Machine CX series works. The CX series has a horizontal, 5-point, high-speed toggle design that aims to bring the best machine performance, and production efficiency to the end users. The model is equipped with Japan-made grease pump, Austrian KEBA I series control and linear guideway supporting injection motion. “Our injection moulding machines are stable, innovative and extremely valuable in terms of our price range,” according to Mr. Long..
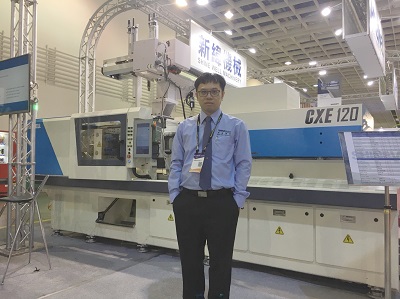
Mr. Long Guo Ren, Shine Well General Manager
FCS Vice General Manager Benjamin Lee said that FCS injection moulding 4.0 solution received good feedback. The FA160 features optimised injection unit and operates accurately with injection close-loop operation control without installing additionally sensors and equipment, and fundamentally upgraded the plastics melt flowing. The technology was awarded the highest prize in the Innovation Award of TaipeiPLAS 2018. In addition, FCS announcement of iMF 4.0 (intelligent ManuFactory) has also won the company the award of excellence in the field of innovative systems. iMF 4.0 will be applied to extract data and values about the moulding parameters, quality control, auxiliary equipment for monitoring and maintenance purposes.
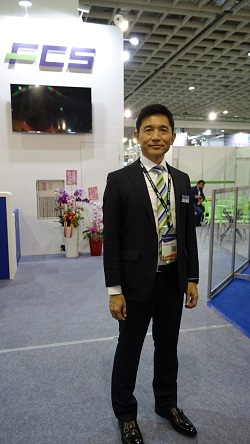
Mr. Benjamin Lee, Vice General Manager of FCS
The winner of Best Design Award was FKI’s eBlow T20s – intelligent full electric blow moulding machine with smart features. The machine is suitable for the food, medicine, agriculture industrial containers and bottles such as 20 litre-bottle types. The machine has the capacity to operate autonomously without the need for manpower, thus reducing costs and energy consumption. FKI CEO & Vice President, Charles T.J. Wei said this is how the company really handles the problems in its customer’s factory, and at the same time refining the design for greater safety and workplace quality.
Kung Hsing, Assistant of President Stephanie Shea said that the company presented a stronger and more energy efficient five-layer co extrusion high speed blown film lines with 15% production boost. The blown film line is targeted for manufacturing shrink films, freezer films and other high quality packaging materials.
PLASCO General Manager, Tony Wang, showed an impressive, neat and sharp monofilament extrusion line capable of producing PP/PA/PET monofilament with filament diameter from 0.12-0.35mm. The application of monofilament products have also been expanded from agricultural and fishery to the textile and sportswear, sports equipment sectors. Reaching high precision is normally the requirement in such industries. Tony said that numerous manufacturers have created solutions to replace multifilament on cloth’s application, and PLASCO plans to be involved in refining monofilament machines used in the textile sector.
Polystar exhibited its recycling machine Repro-Flex reengineered model, an upgraded version that is made more simple and straightforward, and easier to maintain. In addition, Repro-Air was featured. It is very compact in dealing with HDPE and LDPE post-industrial films. Polystar Marketing Manager, David Lo, also shared that the company’s new headquarter and expanded factory will be in operation next year.
Jiuh Kang Sales Manager, Miao-Te Chen, said that Jiuh Kang has been developing multi-purpose application screws applied in injection moulding products for the furniture, construction, chemical engineering and food packaging sectors. One most recent representative collaboration is with Kao Corporation which utilised Jiuh Kang’s large aluminium alloy with a 400mm outer diameter and 2m in length to manufacture personal care products.
Ho Hsing exhibited conical twin screws, counter-rotating twin screws, and mixer screws. Ho Hsing products enable high output and excellent mixing performance given their high precision machining, material excellence, heat treatment and quality control.
Arabplast organiser, Al Fajer Information & Services, was represented by its General Manager Satish Khanna who talked about Arabplast 2019 which will be held at Dubai World Trade Center, UAE from January 5-9, 2019. Mr. Khanna was quite impressed by the technologies showcased at TaipeiPLAS 2018 as he cited that in the Middle East, India Gulf, including Pakistan many of the manufacturers in the plastics and rubber industry have very high recognition of Taiwan-made machines due to their unbeatable value to price ratio, and the stability of operation as well as the excellent services. He believed that Taiwanese machinery producers can tap into the Middle East’s flourishing recycling business as well as bag making sector. This is where the new innovations and upgraded machines can contribute to Middle East factories wanting to reach higher productivity and end-product quality level.
Mr. Satish Khanna, General Manager of Al Fajer Information & Services
Moldmax has begun its technological cooperation with the German senior hotrunner manufacturer Sander, with the key innovation being its valve gate hot runner system which guarantees energy-efficient production; with the particular unconventional design making it easier to opt for productions that requires special shapes, angles of hot runner system, for example in the lightweight, electrical automotive industry.
MING JILEE manufactures recycling machines, sealing and cutting machine, stationery machine, bubble envelope making machine and other niche machines for stationary and bags. The company exhibited the P.E. blown film extrusion line with German Edge Position Controller and automated tension control system. The zipper bag production line is integrated with independent feeding system, along with the tension control we can produce great quality bags. Automated collector at the end of the production line will stack the bags into piles making the production line entirely automated.
CHANG WOEN’s emphasis this year is on its latest machines - the upgraded strength crusher, hydro extractor and squeezer, and so on. The company shared its projects in Thailand, in building a washing line for a supplier to Pepsi. The project is aimed at PET bottle cleaning and recycling, with 5,000 kg per hour, the largest productivity in Thailand. They were excited to identify some the vast arrays of experience to more local and international visitors at Taipeiplas 2018.
Running Shoes & Gear