Blow-molding customers today want new equipment to provide more than an improvement in molding. They need assurance the new equipment will also address current business operational challenges to help them remain competitive in the challenging marketplace. Some of these business issues include: high turnover of staff, need to reduced floor space and high level of vendor support during the machine’s lifetime.
Since 1979, Wilmington Machinery has sought to perfect Rotary Blow Molding (aka “wheels”). From the start, the Wilmington clamping actuation has been simultaneously opposed, which is most desirable for high-quality bottle making. This capability is retained in the new Series III B series—in the four sizes (tonnages) of machines configured for bottle specifications and the quantity to be produced.
The size and capabilities of the Series III B gives molders the ability to replace older and smaller machines on the plant floor with one very capable machine producing the same number of bottles per minute. It also reduces the need to add additional production floor space. Like its Series III predecessor, the Series III B is available with 9-36 molding stations (clamps) rotating in a circular pattern at speeds up to 10 RPM resulting in production of 45 to 720 bottles per minute.
The extrusion unit, as previously mentioned, can be 1-7 extruders dependent upon bottle layer requirements. Die heads include single layer, 3-layer, and up to 7-layer for both single and dual parison molding. The Series II B rotary blow-molding unit (wheel) includes a more robust modular clamping station with pre-plumbed air and water services directly to the clamp platens. This gives molders setup and maintenance times that are significantly reduced.
The new wheel has dual cam clamp actuation that significantly reduces wear on clamp components, allowing for independent open/close control of each mold half. This feature is especially useful in the ejection and placement of a bottle at the discharge point of the wheel. The new wheel retains the “radial positioning” (aka variable pitch) feature that Wilmington pioneered in the 1980’s. A change is the unique “spoke” mounting arrangement of the clamps to the axle. This feature provides for a simpler and more robust arrangement that is much faster to set up. It also retains dual water unions to the molds, providing for improved mold coolant flow and reduced cycle time thus overall cost per bottle.
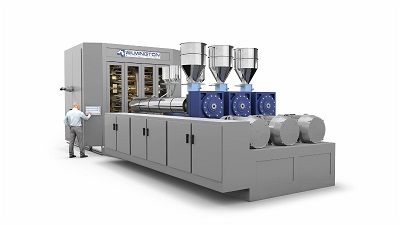
The new wheel also incorporates a servo drive for clamps that provides extreme consistency of the station-to-station clamp opening/closing resulting in the same high consistency in the bottle. The servo drive system is programmed to index the wheel at exactly one station for setup purposes. Additionally,Wilmington’s automatic clamp open/close feature greatly simplifies and reduces the time of mold setup.
The features listed above furnish the molder with direct business operational benefits, such as providing the production team with extra time to spend on other important tasks and reducing the number of staff members needed on floor during changeovers.
Wilmington extrusion systems are produced with the finest commercial components (gearboxes, heaters, etc.) and are known for their modular compact design that Wilmington pioneered in 1979 for the first 6-layer (barrier) bottle programs. The Series III B also introduces Beckoff controls as standard and is production proven on rotary blow molders. With the low unemployment rate and the current difficulty for molders to find qualified workers, purchasing a new machine that is easy for almost anyone with a little bit of training is a necessity. All of Wilmington’s machines include one week of training for the staff. Wilmington Machinery is also willing to train new staff during periods of high turnover.
The new controls provide for improved operator and maintenance friendliness, improved parison profiling, and improved diagnostics. These control improvements in the Series III B ensure high quality molding operations, reduction of energy use, scrap, and much more.
Air Zoom Pegasus EM