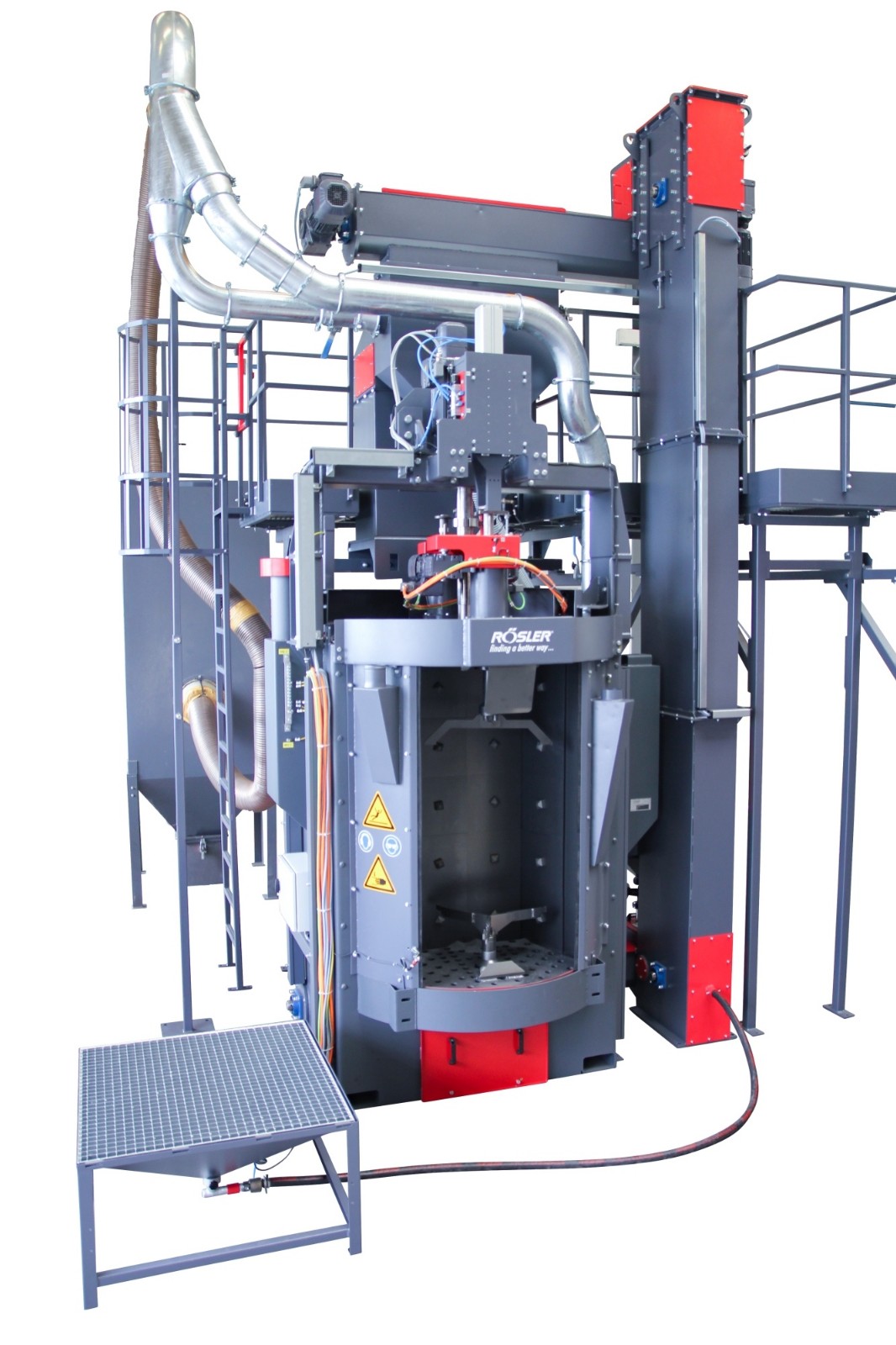
Increasing demand for electric vehicles forces the automobile manufacturers to expand their manufacturing capacities. Among others, this also includes production lines for stator carriers. The surface refinement of these components after the casting operation with a Rösler swing chamber blast machine RWK 6/12-2 must be achieved in very short cycle times within an interlinked manufacturing process.
For the fully automatic de-sanding and deburring of different stator carrier versions the Landshut plant of the BMW group has integrated the swing chamber blast machine RWK 6/12-2 into interlinked, digitized manufacturing lines. The compact dual chamber shot blast machine from Rösler allows the blast cleaning of the aluminum castings within a cycle time of 50 seconds. With the dual chamber equipment concept and robotic loading/unloading the unproductive equipment times could be drastically reduced.
Efficient processing with practically no idle times and a small footprint Within the stator carrier manufacturing line the RWK 6/12-2 – including a part feeding system, robot, a blast media discharge station and a small storage area – requires a space of only 10 square meters. The RWK can handle carriers with a height of up to 1,200 mm and a diameter of max. 600 mm. The work pieces arrive on a conveyor belt from the desanding station, where most of the molding and core sand has been removed from the castings. The robot, placed in front of the shot blast machine, picks up one stator carrier at a time and places it on a special work piece fixture in the chamber facing the load-unload zone. In case of a work piece change the fixture can be exchanged within a few seconds. In the course of the casting process a data matrix code is inserted into the carriers. To protect this code from getting damaged during the shot blast operation, it is protected with a cover. For this purpose the Rösler engineers developed a mechanism that automatically moves the protective cover over the code after the carrier has been placed on the fixture. After completion of the loading stage the chamber turns by 180 degrees. This turn moves the chamber containing the raw part into the blast zone and the chamber containing a finished part into the load/unload zone. The robot removes the shot blasted stator carrier, moves it to the media discharge station for shaking out residual blast media and then places it into an intermediate storage location.
Optimal equipment configuration allows short cycle times
For this application the customer is using a zinc cut wire blast media. The media is accelerated and thrown at the stator carriers by two Gamma 300G turbines with a drive power of 15 kW each. These high performance turbines, developed by Rösler, are equipped with curved throwing blades in Y design. Compared to conventional turbines, the precisely calculated blade curvature generates a much higher media throwing speed. In turn, this results in an up to 20 % higher shot blast intensity and a significantly lower energy consumption. The high blast intensity, combined with the dual chamber machine design, allows cycle times of max. 50 seconds. Another benefit of the gamma turbines is that the special Y design of the throwing blades allows the use of both blade sides. This practically doubles their usable life. With a quick change system, the throwing blades can be replaced without having to dismount the turbine from the housing.
Because of the work piece material (aluminum) and the blast media (zinc), the shot blast machine had to be designed with special protection against explosions. This included special ducting for the exhaust air and an explosion protected dust collector.
Digitization increases process stability and operational safety
In close cooperation with an automation specialist the Rösler engineers implemented a partial digitization of the shot blast machine. For example, a sophisticated visualization of the shot blasting operations and blast patterns of the two turbines allows changing the process parameters during the actual shot blasting process. In addition, the operator can observe "live", which turbine is blasting on which work piece section. If needed, he can initiate changes, reposition the work piece in the blast chamber or modify the blast time. This may become necessary, if, for example, a worn casting mold causes more sand to be deposited on a certain work piece section than defined during the initial programming of the shot blast machine. The operating time is also continuously monitored. After having reached a certain operating hour threshold, the machine automatically provides information about necessary controls and maintenance work, for example, for the throwing blades, work piece fixtures or the protective cover for the matrix code. This helps minimize unplanned equipment down times and significantly increase the uptime of the machine. These are aspects, which are especially important for the cost-efficiency of automated manufacturing lines. Within the framework of its efforts to expand the digitization of its products, by mid 2021 Rösler will present further innovative digital developments in the shot blasting field under the brand name "Rösler Smart Solutions".
For over 80 years the privately owned Rösler Oberflächentechnik GmbH has been actively engaged in the field of surface preparation and surface finishing. As global market leader we offer a comprehensive portfolio of equipment, consumables and services around the mass finishing and shot blasting technologies for a wide spectrum of different industries. Our range of about 15,000 consumables, developed in our Customer Experience Center and laboratories located all over the world, specifically serves our customers for resolving their individual finishing needs. Under the brand name AM Solutions we offer numerous equipment solutions and services in the area of additive manufacturing/3D printing. Lastbut-not-least, as our central training center the Rösler Academy offers practical, hands-on seminars to the subjects mass finishing and shot blasting, lean management and additive manufacturing. Besides the German manufacturing locations in Untermerzbach/Memmelsdorf and Bad Staffelstein/Hausen the Rösler group has a global network of 15 manufacturing/sales branches and 150 sales agents. For more information please visit: www.rosler.com