ILLIG Maschinenbau has lead the way when it first unveiled its innovative IML-T® technology, designed with recycling in mind. The advantage of the newly designed system, developed specifically for the new circular-economy market demands, is the reduction of plastic and simplified sorting for simplified recycling.
The expansion of the IC-RDK 80 thermoforming system by the new IC-RDKL in-mold labeling unit is a further technological milestone in thermoforming, which the company showcased at K 2019. On this IML-T® production line round labels, 92 mm diameter, are manufactured on a 30-up tool. The lids are brilliantly decorated with paper labels. The labels are made out of 0.35 mm rPET. Manufacturing costs of decorated thermoformed lids are 20 percent lower than costs for injection-molded lids since the weight is substantially lower, the output is higher and machine investment is lower.
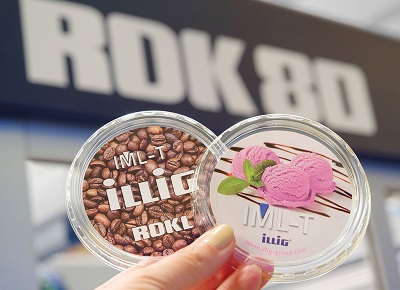
With IML-T® systems the operator benefits from high flexibility due to fast format and tool changes with low tool costs at the same time. Without use of the IML-T® unit the well-known part range can be manufactured on the IC-RDK 80 thermoforming system. So it is possible to also produce smaller batch sizes of IML-T® lids in an economical way. ILLIG is the world's only one-source supplier of IML-T® thermoforming systems (tool and machine) and responds to the increasing market demand for IML-T® applications by presenting these innovations.
Another advantage of the IML-T® technology is that it lets a customer use a different pre-printed label for each cavity, and changing production is also quick and easy. Combined with the high productivity typical of ILLIG thermoforming systems, production of resource-efficient and sustainable packaging is thus possible.