CHINAPLAS, now on a par with K Show in Germany, had a successful run in Guangzhou from May 21-24. The exhibition featured 3,500+ exhibitors from around the world. The exhibition attracted 163,314 visitors with 42,005 or 25.7% coming from outside China, a strong indication of how the CHINAPLAS has become the growth driver in the Asian region’s plastics industry. The whole show floor was alive with machine demonstrations and lively discussions among visitors and exhibitors.
This mega trade show addressed the world’s most pressing issues on the production and use of plastics through its various concurrent events and main highlights. Smart manufacturing technologies & equipment, green & circular solutions to plastics production, and innovative high-performance materials were shown prominently in the 250,000 square meters of exhibition space. With its theme “Innovation is Key to the Future”, CHINAPLAS placed emphasis on the developments in the application of plastics in a wide range of industries such as automotive, packaging, medical, communications, building & construction.
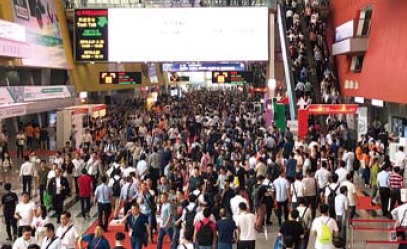
In response to the global trend, a concurrent event called “Industry 4.0 Factory of the Future”, with major players in Industry 4.0, including iPlast 4.0, EUROMAP and Germany’s VDMA were organised with two themed areas –– “Manufacturing Intelligence Control Room” and “Smart Factory” –– which demonstrated intelligent solutions in real-life settings with a daily display of 15 scenarios related to production shop floor, business operations and supply chain management under Industry 4.0 protocols. CHINAPLAS 2019 also teamed up with the Guangdong Industrial Design Association for the event “Design x Innovation”, which comprised of three parts – “CMF Inspiration Walls”, “Design Forum” and “CHINAPLAS Designers’ Night”.
This year, the exhibition identified 10 new materials highlights and 10 processing technologies highlights that will surely define the future of plastics manufacturing. The top 10 new materials highlights include: Fibre-reinforced composites; Lightweight materials for new energy vehicles; Highly functional materials for 5G telecommunications; Graphene-based electrically conductive plastics; Medical grade plastics & silicon rubber with clean, transparent, chemical-resistant properties; High-performance thermoplastic elastomer; Degradable, bio-based and recyclable materials; Additives to reduce VOC emission, change color & brightness; Liquid additives & masterbatches; and New eco-friendly and specialty plastics for 3D printing.
The top 10 processing technologies highlights include: Industry 4.0, digital manufacturing solutions; Cost-effective and high-quality small batch, diversified production; Automatic all-in-one machines; LSR injection moulding technology; Multi-layer injection/multi-layer co-extrusion technologies; All-electric extrusion blow moulding machines; Specialised high-quality film technology; In-mould decoration technologies, combination of PU in-mold coating and flexible manufacturing technology; Recycling Technologies; and Extrusion machinery for medical industry.
Exhibitors’ Feedback
PLASCO Engineering Inc. has been promoting its products at CHINAPLAS and without a doubt, this major exhibition has played a key role in entering the huge Asian market. Tony Wang, General Manager, was present at the company’s booth to meet exhibitors and discuss the company’s products.
As the plastics industry has been focusing on achieving the goals of Industry 4.0 for some years, CHINAPLAS 2019 has put its focus on “circular economy”, which PLASCO expects to be the next big trend. For many years, PLASCO has well implemented measures towards achieving a circular economy by developing extrusion line running 100% post-consumer washed PET bottle flakes, converting PET waste to commodity product such as PET bristle monofilament for broom and brush usage, as well as PET straps for packaging applications. “PLASCO’s successful development of high permanence extrusion line has opened up new potential for recycled PET, which add an extra green touch to PLASCO’s extrusion line, and is of great economic and environmental interest,” Mr. Wang explained.
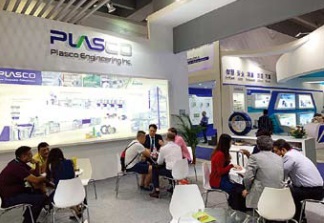
PLASCO Engineering takes its monofilament technology a step higher.
The mechanical demand of monofilament used for technical fabrics has increased. Through PLASCO’s technical expertise and extensive experience in the field of monofilament extrusion line, the new development in bi-component (bico) monofilament extrusion was planned, developed, and was already found to be extremely versatile that it allows numerous material combinations for various applications.
“The bico monofilament technology brings the functionality to monofilaments. The two polymers constructed monofilament able to develop special properties achieve dimensional stability, strength, elasticity of the core as well the lower melting temperature or special surface properties of the sheath,” Mr. Wang stressed.
KRAIBURG TPE showcased the latest automotive and consumer products TPE innovations. In particular, it launched its groundbreaking automotive low odour and low emission TPE material that is expected to bring better interior air quality to automotive designers and manufacturers to help improve automotive manufacturing standards. At the same time, KRAIBURG TPE has also introduced TPE compounds that meet China's new national standard (GB). These food safety grades can be used in a variety of applications such as consumer products, food packaging and toy industries, in compliance with China's strict local regulations and standards.
Mr. Roland Ritter, Director, Asia Pacific at KRAIBURG TPE said that "thanks to the excellent quality and continuous innovation of the products, the company's Asia Pacific including China market performed well last year and is expected to continue to grow this year. The company is evaluating its presence in the Asia Pacific region with the possibility of adding a sales office in the district."
Speaking on the competitive advantage of KRAIBURG TPE, Mr. Ritter said: “We focus on international business and provide products that meet international quality standards. In effect, we never sell products, as our model is to continue to help customers solve problems and provide solutions to their problems. Most importantly, we have always relied on product quality, and the product qualification rate is as high as 99.5%." In response to the needs of current customers, Mr. Ritter believes that due to fierce competition, manufacturers urgently need suppliers to provide innovative technologies and products to help them continuously improve environmental protection and energy conservation, while maintaining or even increasing production capacity without increasing production costs.
Oman Oil and Orpic Group's Polymer Marketing Division introduced its enhanced performance and cost-saving to support China's economic prosperity, innovation, sustainable development and vitality. “This year is the first time for Oman Oil and Orpic Group to participate at CHINAPLAS. We are very pleased to present our latest innovations in the field of polypropylene to our customers in China at such an industry event,” Chief Commercial Officer Talal Al-Awfi said.
Oman Oil and Orpic Group is a comprehensive energy company focused on sustainable development, providing fuel oil, chemicals, aromatics and polymer products to the world with superior business capabilities. It is one of the largest companies in Oman and one of the fastest growing companies in the Middle East oil industry. Its Polymer Marketing was founded in 2017 to provide innovative polypropylene (PP) solutions to markets and customers in more than 60 countries. Group Chief Commercial Officer Talal Al-Awfi stressed: “The debut of ORPIC at Chinaplas reflects the company's commitment to continue to develop existing and future technologies based on the needs of Chinese customers. With more than 10 years of experience in the polyolefins industry, the Group has the ability to provide sustainable, valuable plastic solutions that help address global challenges such as climate change, food protection, healthcare and waste disposal."
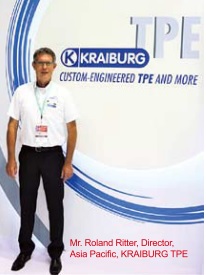
Oman Oil and Orpic Group recently opened a Northeast Asia office in Shanghai, which is committed to bringing polymer marketing company services to customers in Northeast Asia. The Group is incorporating random copolymers and block copolymers into the polypropylene product line, and will add high-density polyethylene and linear polyethylene product lines to the product portfolio to provide more innovative solutions.
Arburg showed the Chinese audience the new customer portal, the potential of Augmented Reality (AR) in the service industry and digital assisted systems. “Digital transformation is the focus of our attention for many years,” said Gerhard Böhm, Sales Director of Arburg's Germany headquarters. “Our main purpose this time is to show customers how to use Arburg's innovative solutions to serve injection molding, with special attention on additive manufacturing and automation, and how to cope with the digital future of plastics processing," according to Mr. Böhm. From digital-assisted software packages to preventive maintenance and remote services, from the new portal service website to the company's own MES system, as well as the central production management system ALS, Arburg shows off all aspects of IT networking and more efficient production of plastic parts.
At CHINAPLAS, visitors witnessed how all machine exhibits on the stand were connected to ALS. The three main products include: a liquid silicone rubber processing system for the production of ready-to-use LSR/LSR watches, a gold-plated motor Allrounder for medical technology, and a Freeformer 200-3X for industrial additive manufacturing. All three machines are networked via the Arburg Central Production Management System ALS. The site was subjected to the most onlookers of the two-component liquid silicone rubber processing system, and Arburg showed how to “make a moulded” LSR watch. The hydraulic two-component Allrounder 570 S has a clamping force of 220 tonnes and two injection units arranged in an L-shaped position, which automatically produces two two-colour straps in a 70 second cycle time.