A radical review of your shop''s manufacturing processes can achieve a dramatic improvement in productivity and workflow. Looking at all aspects of your business involving all staffs and subsequently introducing a program of training can result in a greater degree of multi-skilling on the shop floor including investing in machine tools. However, one of the biggest catalysts for change is a review of your cutting tool applications.
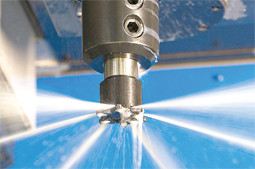
Price The price of a cutting tool equates to the cost of the process. When you compare the price of a high performance CBN tool to the price of a general purpose carbide insert, you may assume that the high performance tool is less economical. In truth, the high performance tool may or may not be the right choice but the price is too small a factor to make that determination. While the cutting tool's price does add to the cost of the process, the same cutting tool also subtracts from the cost of the process through savings in various areas. To make the point even more clear, consider that a machining facility is not delivering a tool to its customer梚t''s delivering a part. Therefore, the cost of the part should be the focus. The price of the tool is such a tiny portion of the cost of the part that it is actually very easy for a high-performance cutting tool to bring the overall cost down. The price of tooling is actually an ineffective place to look for savings. Would you rather have a 30 percent savings on your cutting tools or a 20 percent increase in cutting speed? The analysis shows that the right choice is not even close. Assuming the baseline cost of the part is $10, the reduced tooling cost would save only 9 cents. By comparison, the increased speed would save 16 times that much, even after assuming that the tool that achieves this speed increase is 50 percent more expensive. Try that same analysis with a tool that costs two times or three times as much as the baseline tool. It can easily be shown that even very large increases in tool cost do not affect the savings resulting from even conservative gains in productivity. In addition, some shops apply high-performance tooling to achieve levels of savings that are truly off the chart. Tooling engineered to provide both long life and high reliability can make it possible for shops that have never done so before to achieve successful "lights out" machining processes. If the shop can run unattended after hours, capturing machine capacity that is not even being used today, then arguably the costs of both labour and machinery for this work drop to zero. After all, no operators are present, and the machinery has been paid for by the daytime machining. That is why unattended machining can be one of the most profitable ways for a high-performance tool to transform the machining process. Meeting increased demand
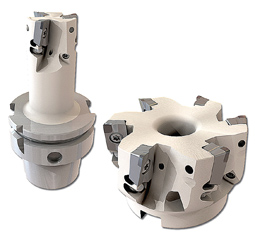
Three years ago, the industry was moving forward at a very fast pace and, and most companies find it difficult to keep up with the increase in demand. Some were faced with a choice of replacing a number of their existing machine tools in order to increase productivity, a route that would have been prohibitive due to the cost. This option is based on the assumption that some existing machine tools would not be able to cope with the demands of modern cutting tools. It''s best to try a new generation of cutters on the machines you have. Utilising the machines you already had, investing in new tooling and increasing the feeds and speeds will make a significant improvement in your manufacturing capacity, work-flow and delivery performance. The added bonus is that eliminating many operations by using the next generation of tooling, such as milling cutters, multifunction eco-cut tools and driven tool-holders will open up many machining possibilities, while reducing non-cutting time and work in progress. The tooling will also
Artículos deportivos para ni?os