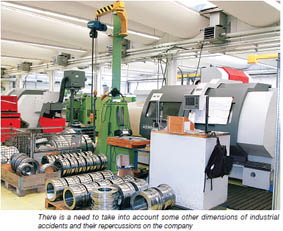
A danger foreseen is half avoided
Source: Release Date:2009-09-23 137
Add to Favorites
Ask any plant manager on the most stressful moment in his professional life. In all likelihood, the reply would be an accident or injury to an operator or a colleague. In this day and age of ''too many things to do and too little time,'' sometimes the job of keeping a manufacturing plant safe takes a back seat to rolling out products. Those who have been in the industrial sector for quite some time would recall that industrial safety and security is generally emphasised in two situations. One, where someone has been injured and the plant is scrambling to eliminate the hazard. Or two, the plant is being proactive to identify potential risks and is taking steps to reduce these risks before accidents happen. It''s pretty obvious that it is better to be in the latter category. Safety is important That employee safety is of paramount importance is a known fact. However, one also needs to take into account some other dimensions of industrial accidents and their repercussions at the organisational level. These are: Compliance: Adherence to safety standards and codes is no longer seen as a mere testimony of corporate commitment to abide by local laws. It also brings in other benefits in terms of standardised, high quality sourcing and streamlined processes. Downtime: As organisations increasingly aim at maximising output by utilising optimal existing resources, any equipment downtimes is a serious blow to topline targets. This also applies to a skilled operator's absence owing to serious injury or accident at the plant and the ensuing production loss. Overall equipment efficiency: Frequent equipment shutdowns have as much a negative impact on overall equipment efficiency (OEE) as incorrect operational practices and component replacements. In fact, many organisations today track OEE as a key metric of production line performance. Return on investment: Given the trend of high interest rates in the country, capital expenditure is often the most watched upon figure on company balance sheets. As corporate intend to amortise fixed costs over a longer period, lifecycle costs of the equipment becomes an important consideration versus outright purchase and installation cost. Needless to add, safe operation of equipment bears a heavy weight while measuring return on investment (ROI).
Operating expenditure: In terms of margin pressures, every organisation has a close eye on containing operating expenditure (OpEx). With budgets getting tighter every year and rising materials and manpower costs, the last purchase you want to approve is the one related to plant accidents or injuries. Minimising risks With limited in-house technical expertise, how does one go about minimising such risks? Here's a stepped safety lockout plan: Step 1: Understand the laws, regulations, policies and standards The first step is to have a clear understanding of what laws are in force and what parties are responsible for what duties. It is prudent to check both national and local laws, as well as local codes. Have a clear understanding of your plant's position and responsibilities by talking to corporate counsel and checking company guidelines. Plant and employee safety accountability could rest with the plant manager or a safety manager, depending on company policies. Of late, most organisations have established a dedicated health, safety and environment function to focus on occupational health, site safety and environmental sustainability. Step 2: Understand what equipment is potentially dangerous The second step is to understand which equipment is potentially dangerous and plan to reduce risks, if any. The best way to accomplish this is to walk through your production facility. Have a picture in mind of how you want to categorise your plan. Organise your plan by machine, by production line, by area, by function, or by whatever categorisation that makes the most sense for your plant. IdentTienda outlet deportiva
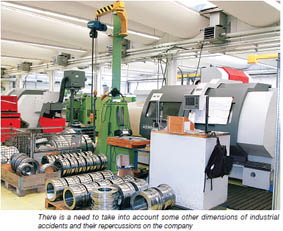
Add to Favorites
You May Like