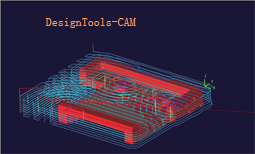
Design tools for rapid mold development
Source: Release Date:2009-09-28 103
Add to Favorites
Moldmakers face an increasing number of challenges that impact virtually every facet of mold development. Shorter leadtimes, pricing pressures that push down profit margins, and demands for higher levels of quality and longer duty cycles, have substantially altered the paradigm for winning in today's moldmaking industry. Producing molds faster, cheaper, and better is the current mantra for moldmaking success, and moldmakers are continually evaluating mold design tools and technologies that can help them achieve these goals. Evaluating mold process
Examining the mold development process itself is equally important for determining how specific tools and development platforms can benefit a moldmaking operation. Such an assessment will reveal a fact that most moldmakers already know: the single aspect of the mold development process with the most potential for timeand money-saving productivity gains is the interplay between moldmakers and part designers. It's this backand- forth interaction between the customer who designs the part and the moldmaker who has to create the mold to produce it that holds the greatest opportunity for realizing the improved efficiencies moldmakers need to save time, reduce costs and maximize profits. Although some manufacturers follow a concurrent strategy that encourages part design with an eye toward mold development, part design and mold development are typically separate, sequential processes for the vast majority of products. From the initial handoff of the part design to the moldmaker through evaluation of moldability, changes related to production issues, estimating, quoting, and incorporation of in- process design changes from the customer, the interaction between part designers and moldmakers is a highly iterative process that is fraught with opportunities for delay and unanticipated cost. An easy-to-use, flexible 3-D CAD system that includes design automation/ communication, parametric modeling, and surfacing/geometry manipulation tools can bridge this gap梡roviding maximum benefits to moldmaking operations. Managing diverse data The first step in the mold development process梤esponding to a request for proposal (RFP)梤equires moldmakers to import, diagnose, and repair part geometry in order to assess its suitability for injection molding, develop estimates and produce a formal quote. Moldmakers need to complete this step before even winning the business; it behooves them to accomplish this as quickly and costeffectively as possible by using a 3-D CAD system with broad model import and geometry manipulation capabilities. Of course, the best scenario is to use the specific CAD package that most of the moldmaker's customers use to design parts, so the mold designer can simply open the file. However, because customer parts can range from 2-D drawings and neutral file formats梥uch as DXF? DWG, IGES, STEP, ACIS?and Parasolid畻to file formats that are native to specific 3-D CAD systems, using a CAD platform that can import the widest set of diverse data formats directly, or through file conversions, provides a real advantage. In addition to offering capabilities for diagnosing imported geometry in states of disrepair, CAD systems that include tools for repairing geometry errors have become increasingly beneficial. For example, mold designers need the ability to remove rounds and re-trim edges after removing rounds, especially when adding draft to improperly drafted parts. Moldmakers also may encounter complex model geometry with gaps in surfaces, for which they will need advanced surfacing capabilities, such as an in-sided surface patch, which allows mold designers to fill in a surface tangent to a space defined by any number of boundaries, or the ability to pull on a point in a network of curves to modify a surface. At minimum, mold designers need access to round, draft and surfacing capMax 90 Winter Sneakerboot
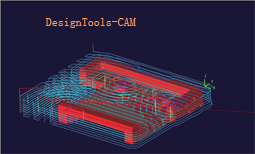
Add to Favorites
You May Like