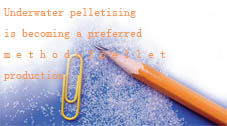
The evolution of underwater pelletising
Source: Release Date:2009-09-23 138
Add to Favorites
Underwater pelletising is becoming the most preferred method of pellet production over other processes available in the world market today. Underwater pelletising is in the family of die face pelletisers. Some types of die face pelletisers use only air for cooling and transporting the pellets. A variation of this type of pelletising uses some water spray or mist to start the pellet cooling process and to prevent pellets from sticking together. Another type, water ring, pelletises entirely in the air, but as the cut pellets centrifugally leave the die they go directly into a high velocity water stream circulating inside the cutting chamber, but not touching the die. The pellets are then de - watered and dried by means of centrifugal pellet dryer. Gala has been a leader and innovator in the realm of small production machines (from 10 kg/h to 15,000 kg/h) and has launched pelletising machines that have enhanced the process. The Gala underwater pelletising system is a continuous closed loop system consisting of the underwater pelletiser, the tempered water system, a centrifugal pellet dryer, and the electrical control system. The process begins at the pelletiser''s die plate (temperature controlled) with a symmetrical pattern of die holes arranged in one or more concentric circles. The die plate is connected with the upstream extruder or melt pump and receives the molten polymer under suitable pressure. Since the die plate is completely submerged in the process water during operation, it is important that the die plate is well insulated against the cooler process water temperatures. A water system maintains a temperature controlled water supply that is cycled continuously through the underwater pelletiser.
The cutting blades of the underwater pelletiser are rotating and cutting the molten polymer as it emerges from the die plate into the process water. All of these take place in a cutting chamber or water box where pressurised process water keeps the newly formed pellets from sticking together, provides instant cooling, and transports the pellets to a centrifugal pellet dryer. The centrifugal dryer dewaters the pellets and mechanically bounces the pellets against stationary screens so the surface moisture is knocked free of the pellet. Internal latent heat of the pellet and countercurrent air flow aid in the drying process. Pellets entering the bottom of the dryer take an upward and spiral path through the dryer and discharge out of the top within a few seconds. Moisture levels of 500 ppm or less can normally be obtained. Higher demand for small underwater system Underwater pelletising was very well known because most polyolefin plants had been producing pellets using this method for some years. As new plants came on stream, the production rates also increased. Each new plant produced more than the previous. Ten tonnes per hour was once thought to be a fair capacity, but that quickly changed to 20 tonnes, 30 tonnes, and higher. During the 1960''s and 1970''s the production capacities were reaching 50 tonnes per hour. This growth spurt was instrumental in Gala''s entry into manufacturing of small underwater pelletising systems. The extruder manufacturers for these large polyolefin plants also made their own underwater pelletiser in order to provide a turnkey package and to protect their individual intellectual knowledge. As these manufacturers increased their machine sizes to handle the ever increasing production rates being demanded, they soon left behind their interest in manufacturing small underwater pelletising machines. As Gala listened to its customers, it was encouraged to enter the small underwater pelletiser market because there had been few options except for strand pelletisers, and dicers and hot face pelletisers for some processes. The compounding and additives market liked underwater cut pellets because they could produce pelletsNike Mens Shoes
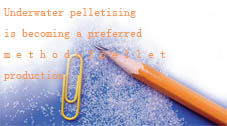
Add to Favorites
You May Like