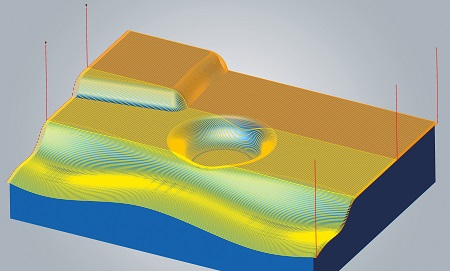
Enhancements are to programming tasks, and also to make machining quicker and simpler. The new 3D and 5-axis corner rest material strategies guarantee the efficient machining of rest material in corners. What’s even more promising is that optional modules – hyperMILL® ADDITIVE Manufacturing and hyperMILL® VIRTUAL Machining – offer groundbreaking technology, simulation, optimization, and connectivity solutions consistent with key directions of modern manufacturing.
hyperMILL® 2020.1 provides an innovative approach to reduce rest material in corners after roughing tasks. The 3D and 5-axis corner rest machining strategies bring together parallel and Z-level rest machining toolpaths into an optimal process. 5-axis corner rest machining makes indexed machining of difficult to reach corners possible. Automatic inclination selection, simultaneous linking movements, and collision avoidance are available in this process. A further example of increased efficiency is 5-axis turbine blade tangent machining with the conical barrel cutters (also called circle segment or parabolic end mills) co-developed by OPEN MIND. Top milling with these tools makes higher feedrates possible and allows a more even surface quality to be achieved.
Simplified programming
Reducing programming times in line with practical requirements is an important motivation in further developing hyperMILL®. A new tool path splitting option enables you to automatically split long tool paths according to a specified time or distance. This is essential when cutter life is an issue while machining hard materials. This procedure reduces the need to modify programming jobs into smaller regions or the added risk to manually edit tool paths to account for tool life. Now the hyperMILL® system can account for tool life and schedule the tool changes. Mill-turn tool paths can also be split to account for tool life or based on cutting technique. Features can be automatically identified by hyperMILL® to enable inside, outside, face or grooving tool paths.
Controlling additive manufacturing
As was already announced at some trade fairs, hyperMILL® ADDITIVE Manufacturing in version 2020.1 is now available. OPEN MIND is thus offering a piece of software that can even be combined with additive or hybrid machine tools.
The hyperMILL® VIRTUAL Machining Center also boasts new features. The Optimizer module – which allows a CAM program to be perfectly adapted to the machine’s limitations during postprocessing, for example – now supports the “Smooth linking” function. This automatically optimizes all linking movements between the individual operations during postprocessing. This ensures that repositioning and movements are always in close proximity to the workpiece while also being checked for collisions – making programming with the job linking obsolete.
Another new feature from 2020.1 will be that users can independently make small automation tasks a reality with the help of the hyperMILL® AUTOMATION Center. The hyperMILL® AUTOMATION Center serves as both a development and runtime environment. This allows you to automate the joblist creation process and the selection and positioning of the clamping device, as well as define a uniform process for all programmers.
Air Jordan VIII Low