The Whitebloc Filling System Aero has been specially designed to be used for bottling Extended Shelf Life (ESL) beverages, according to GEA. The new filling technology has been developed with the benefit of GEA’s extensive experience in aseptic filling to inspire the design.
In recent years, a key trend in the market for dairy products has resulted in the demand and consequent development of a wide range of high-quality dairy beverages with a prolonged shelf life compared to fresh products, with an increasing request in both developed and emerging markets.
The new Whitebloc Aero uses proven technology that has been optimized to meet the specific needs of producers of ESL beverages, that often focus on small batch production, to give them the edge in a competitive marketplace. GEA says these include simplicity, efficiency, reliability, practicality, sustainability, flexibility and the lowest possible Total Cost of Ownership (TCO).
Compact simplicity and efficiency
Sensitive, milk-based ESL beverages need special requirements to preserve their shelf-life and organoleptic properties. As such, container decontamination is an essential part of the process to ensure an effective and reliable extended shelf-life in cold chain distribution.
The GEA Whitebloc Aero’s design is optimized for the treatment time required in ESL applications; this allows bottle decontamination with dry H2O2 and subsequent activation with warm air to be performed on a single carousel which keeps the layout as compact as possible.
The decontamination, filling and capping processes are performed in a simple hygienic cabin with a top-down laminar flow of sterile air with a slight overpressure to maintain a clean and protected environment.
Speed and flexibility
The ESL market frequently requires producers to run small batches and fill a variety of products on the same machine. The GEA Whitebloc Aero offers the typical production rate of fresh and ESL applications, using both PET and HDPE containers with plastic caps or aluminum foil closures and using neck or base handling. The machine can be supplied in a standalone configuration or, for PET bottles, combined with a stretch blow molding machine.
The GEA Whitebloc Aero can achieve a wide range of decontamination targets depending on the required level of product sensitivity and shelf-life for both high and low-acid products. Equipment cleaning is fast, cost-effective and flexible thanks to the possibility to choose between the integration of customers’ existing fluid cleaning system or a dedicated cleaning process skid unit embedded with the GEA Whitebloc Aero.
A built-in product recovery system eliminates product waste during the start-up cycle, at the end of production and during changeovers. Filling valves can be equipped with a load cell (weight filling) or flow meter (volumetric filling) to meet the various requirements of the liquid dairy product market.
Environmentally sustainable No water is used in the process so producers can be confident that production is not wasting scarce natural resources. Both bottles and closures are treated using the same chemical for maximum convenience and consistency.
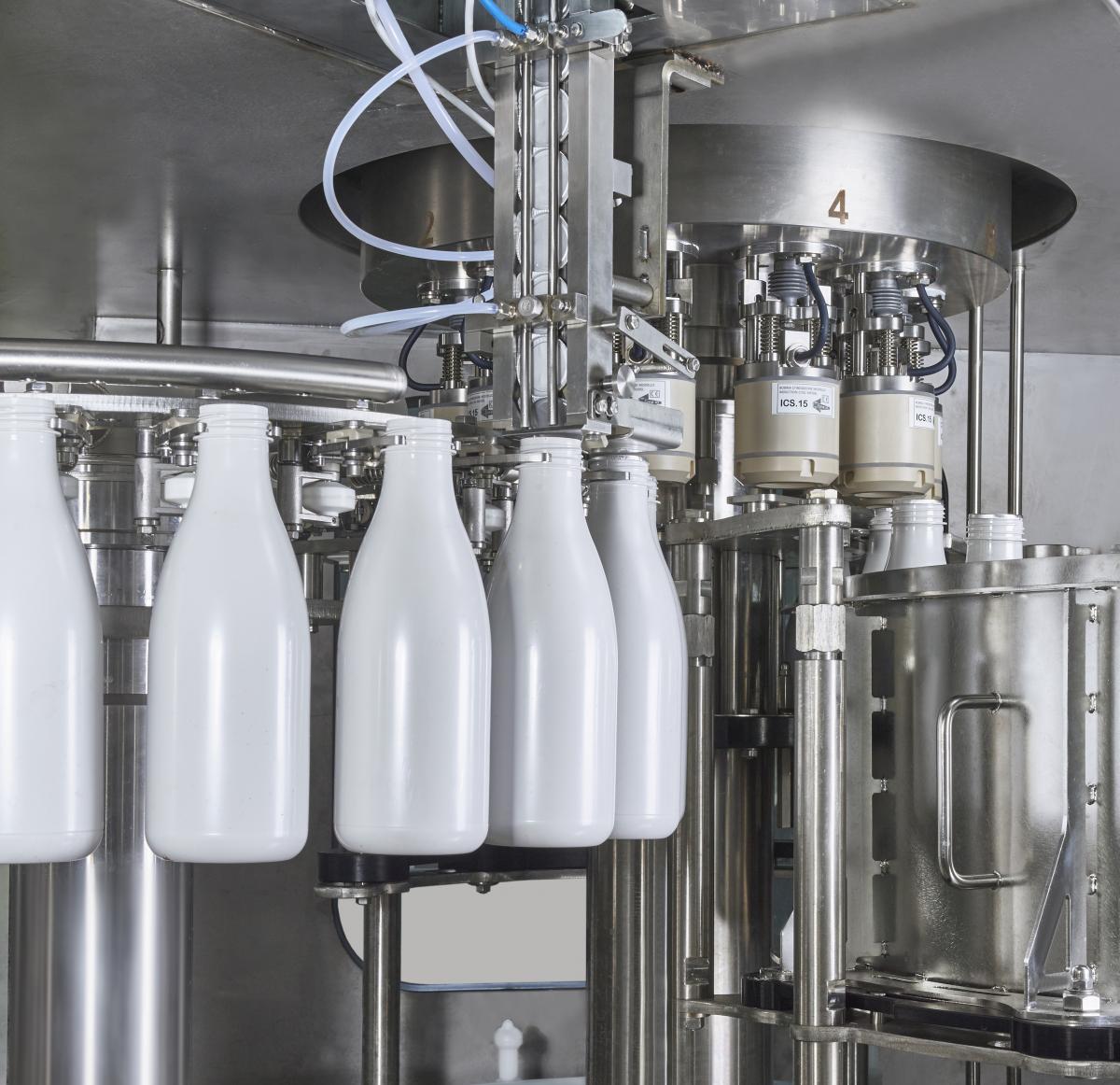
Aerobloc Filling System for fresh beverages
As part of the newly launched Aero platform, GEA has also developed a filling system designed specifically for fresh beverages: the Aerobloc Fresh. This is a hygienic filling platform for milk and liquid dairy products with a short shelf-life, without requiring any container decontamination. Its versatile, modular design allows the option of adding a synchronized stretch blow molding machine or an air rinser and/or a neck trimmer to meet the specific requirements of the product and container material.
Together, the Whitebloc Aero and the Aerobloc Fresh complete the range of advanced filling equipment for ESL and fresh beverages from GEA as end-to-end dairy processing single-source supplier. They have been designed based on the wide GEA’s expertise in handling aseptic and sensitive products yet keep the simplicity, flexibility and reliability producers expect. With the benefits of GEA’s global Service support and strong local technical team, customers can feel confident that their processing and manufacturing infrastructure will work to help ensure their continued business success.