K 2019 is getting closer and the recycling world is getting ready for an event full of innovations. As always, FIMIC will offer something new to its customers this year. The recycling sector constantly demands increased productivity and higher quality, but often technology can’t withstand high levels of contamination or high hourly production. The limits of recycling machines remain evident, but the quest for circular economy demands actions to save the earth. FIMIC is strongly motivated by these new factors, which lead to a strong demand for new filtrations and new technologies for post-consumption in Europe and worldwide.
For this reason, FIMIC has decided to develop new technologies to allow the customer to choose the filter according to the final application, the filtration, the material to be processed and the hourly production. Based on these parameters, FIMIC is currently able to supply 5 different types of filtration with 5 filter models. It will be the only company on the market that is specialised in filtration and counts such a diverse range of models.
FIMIC is currently well known worldwide for its RAS filtration model, which will soon reach 300 units, installed not only in Europe, but all over the world, from Chile to New Zealand. The RAS system is a scraping filter known for its flexibility and strength! This filter, through the use of two blades, is able to scrape very high contaminations (for example up to 15% of paper) and also contaminations blocked by a laser or punched mesh. This type of filtration, from 80 to 2000 micron, allows the customer to choose the quality of the filtration and to keep an eye on the operating costs.
FIMIC retains the record for the lowest operations costs compared to all other filters on the market. Furthermore, FIMIC offers five different filter sizes. To give an example, these can reach 350 kilos of LDPE with the smallest diameter (Ø325) and 3.000 kilos of HDPE with the largest diameter (Ø700). These great results have obviously been achieved by great entrepreneurs, who have allowed FIMIC to constantly improve and develop.
Over the years, not only filtration has been integrated with the laser screen making it possible to reduce the filtration range below 300 microns, but also new blades, new scrapers and new sealing systems have been developed. All of these could happen thanks to the FIMIC team, which over the years has developed so much that it now counts 22 operators, including 5 technicians, and installers.
As mentioned, the world of recycling currently requires automatic machines that can reach a higher quality with ever lower material waste and minimum operating costs. Even the waste can be adapted, based on the amount of contamination that occurs within the material.
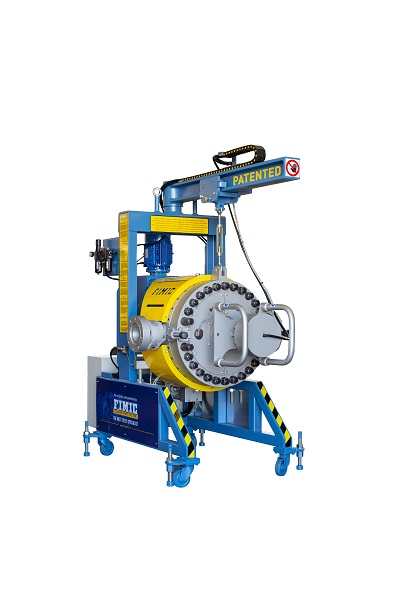
In fact, the RAS model can work both post-industrial and post-consumer materials thanks to the waste regulation system and to a closed valve that opens only when needed and for a set time. The FIMIC team can test the material. The company has a Ø105 extrusion line and a laboratory extruder to verify the filtration level that can obtained in case of film recycling. The progress that FIMIC has experienced in the last few years has not stopped yet. The RAS model was itself an evolution of the first FIMIC REF model. REF is in fact the FIMIC counter-flow model, but it has hardly been used in recent years, as it has been superseded by new technologies that result in lower amounts of waste material and a longer usage of the filtering mesh. In fact, the REF model is currently combined with the RAS model, giving life to the RAS + REF filter.
Some countries prefer to keep this technology as an ace up their sleeve for extremely clean materials. For this reason, out of the 55 filters sold per year, FIMIC still keeps a couple of REF filters.
By having just one filter, the customer can decide to move from one filtration system to another by changing the components inside it. It is like having two filters in one!
For the lovers of the mesh screen, however, in addition to the REF system, FIMIC has developed an additional filter, the TEN model, which is in the final testing phase with a trusted customer. This filtration system provides a continuous roll mesh filtration, which is automatically replaced when it is clogged.
Clearly, FIMIC continuously improves current systems and, for this reason, any accumulation system has been removed in order to avoid the creation of gas inside the material. This filtration system is also properly explained in a video published on YouTube where you can notice how simple it is: at the time of the change a basket rotates the continuous belt screen in tension, acting as a support for the filtering mesh.
The system therefore allows the interchange through a piston that automatically releases the screen at the time of its exit, obviously maintaining the tightness and avoiding the breaking of the screen.
In fact, the increase in contamination over the years has led FIMIC to develop a double filtration system with two phases: a coarser first and finer second. This new type of filter, unique in its kind, eludes the need for a double passage thanks to a cascade extruder. Therefore, the installation of two filters, the installation of a gear pump or the presence of two separate filtration machines is not necessary.
For highly contaminated materials (composed of both large and thin contaminants) the ERA filter, makes it possible to insert a single machine with two separate filtration chambers inside of it, in any extrusion line, cascade or not. The first chamber can be integrated with a >400 microns punched filtration, so the cheapest screen will block the largest and most aggressive filtrations. It is also possible to use the laser filtration in the first screen (<400 microns) to eliminate the thinnest contamination in the first phase.
In this way, in case of a coarse first filtration, the second one can guarantee a finer filtration, e.g. 150 microns. The laser filter will be protected by the punched filter in the first filtration chamber. In the case of a first laser filtration, the second one can also be a laser filtration and a higher quality can be guaranteed thanks to two fine filtrations.
Keep in mind that the ERA model is equipped with two independent discharge valves, which will adjust the percentage of discharge according to the effective contamination. The flexibility of the ERA filter therefore allows not only to work with the Laser - Laser or Punched - Laser but also to adapt it and use a single filtration chamber, making the ERA a RAS filter! This model has already been installed on several occasions and we trust in further installations soon.
Last but not least, we can finally talk about the innovation that will be presented at K this year in October in Dusseldorf.
Bear in mind that the RAS model has 5 different diameters that can be adapted to the extruder according to the hourly production, plastic material to be recycled, and the filtration for the final application needed. Unlike its competitors, FIMIC reaches a filtration of approximately 4,000 cm² with a single screen. Thanks to this particular filtering surface, FIMIC has managed to reach very high production rates with very fine filtrations, for example 2.000 kilos of LDPE per hour for film application at 100 micron, or up to 3.000 kilos per hour for HDPE MFI 0.5 material with 200 micron filtration.
In some cases, however, the market requires higher quantities than those already achieved with the current productions. Furthermore, FIMIC always wants to guarantee the lowest possible pressure so that the contamination is effectively blocked by the screen and, also, to avoid that the contamination pass through the drilling of the screen because of the excessive pressure.
For this reason, FIMIC always tries to guarantee a high filtering surface, which increases the quality of the final product and does not degrade those materials that are sensitive to temperature and pressure, such as LDPE.
In view of an increasing production and more complex material in terms of filtration and MFI, FIMIC has developed a new filter: the GEM model. GEM derives from Gemini. For the first time FIMIC produces a filter equipped with two screens to guarantee a greater filtering surface than that of the RAS700. In this case, there will have two screens and two discharge valves, guaranteeing a filtering area of 5,552 cm² with a single machine. This innovation will increase the extruder production keeping the highest quality of the final product, while guaranteeing the simplicity that distinguishes FIMIC and the maximum reduction in the cost of operation.
Most importantly, the market does not offer the possibility of having only one machine, only two screens and only two valves that guarantee this filtering surface. This will not only allow shorter residence of the material, lower energy consumption and lower consumption of spare parts, but also less waste and a more efficient and faster replacement of the screen. FIMIC is therefore waiting for you at the K not only to admire this new filter, which makes FIMIC the only company to have 5 types of automatic filters adaptable to any extruder and any application, but also to see two of the models on display, RAS and ERA, in the stands of extruder manufacturers with whom we normally collaborate.
FIMIC guarantees support and assistance even for new lines, with Italian or foreign contractors. Five electrician, mechanics and installers will be available to you to guarantee the commissioning of your FIMIC automatic filter.
New Balance Popular Collection