如何把握工件的同心度?本文,世界机床工具行业领航者哈挺公司为您介绍主轴、夹头中的同心度,并对加工操作中导致夹头加速磨损的问题$
The machine spindle, collet and machining process all contribute to the workpiece concentricity - the degree to which a given dimension resembles a perfectly round circle or cylinder. There are several areas of concern when trying to achieve the best workpiece concentricity possible. Hardinge, a machine tool builder of super-precision turning centers, has noted down this article to show you the concentricity in the spindle, concentricity of the collet, the exact collet size for optimum concentricity, machining operations that cause collets to wear faster and lose concentricity, and other causes of wear on multi-spindle machines.
Concentricity in the spindle 1. TIR of the spindle angle-if the spindle angle does not run concentric, it is impossible for the collet and workpiece to run concentric.
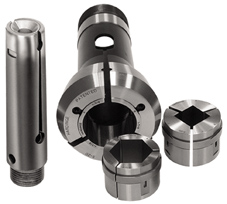
2. TIR and wear of the spindle back bearing-if the back bearing of the spindle is worn, it will allow the back bearing of the collet to pivot, which will cause excessive runout. 3. Runout of the spindle drawbar-if the drawbar is not concentric and square with the head angle and the gripping area (order hole) of the collet, the pressures will be exerted on one leaf of the collet instead of all three. The parts manufactured with this collet will not be concentric with the chucking diameter. The uneven forces on the collet leaves may cause them to break. Hardinge offers a superior spindle that is capable of maintaining a high degree of concentricity that equates to actual part roundness guaranteed within 15 millionths (.38 micron) on specific machine models. Concentricity is very dependent on spindle design. It can best be maintained by following a regimented machine maintenance program and by selecting the most appropriate workholding product for each individual job application. For best results use the proper collet gripping (order hole) size, use cutting tools that are properly sharpened and centered, and use proper feed rates and spindle speeds for the tooling and material selected. Consistent use of abrasive materials and/or heavy machining operations can wear the spindle. If this is the case the spindle can be rebuilt if required.
Concentricity of the collet The TIR of the back bearing, the head angle and the threads apply to the collet, and spindle. Collet concentricity is measured by putting a gauge pin in the collet gripping area (order hole) and measuring the Total Indicator Reading (TIR) of the pin's runout with a .0001-inch dial indicator at a specific distance from the face of the collet. Hardinge guarantees .0005-inch (.0127mm) TIR for standard 5C round collets with a gripping area (order hole) up to .1875-inch (4.76mm), .001-inch (.0245mm) or better for a gripping area (order hole).188-inch (4.77mm) and up, and .0002-inch (.005mm) for all special accuracy round collets.
Use exact collet size for optimum concentricity Collets should be ordered to the exact size of your stock. If you have stock variations choose the average diameter. When the collet is the proper size for the workpiece, there is full bearing along the angle and the circumference of each segment of the collet where they mate with the spindle angle (seat). The result will be good concentricity and excellent holding power. If the collet is oversize the part may pivot at the line of contact. The turned diameters may not be concentric with the bar or chucking diameters and the machined diameters can be out-of-round. There will be line contact at the center of the leaf. If the collet is undersize, the contact will be at the top of the head angle on the spindle angle and the collet. This can help with bar push-back because the more tool pressure exerted on the bar, the tighter the collet becomes. The part may pivot around the point of contact when excessive chucking pressure is NOT applied. The tur
Air Max 2017