五轴加工中心在加工较深、较陡的型腔时,可以通过工件或主轴头的附加回转及摆动为立铣刀的加工创造最佳的工艺条件,还可以提高模具的"
Five-axis machining centers do not just move in the linear axes X, Y and Z. Instead, these machines also move in two rotary axes, often identified as A and B. The rotary axes tilt the tool with respect to the part. Physically, it can be either the tool that tilts or the part that tilts. Different machines accomplish the rotary motion in different ways. Some machines move the rotary axes only to position the tool or work outside of the cut. This is referred to as 3+2 machining. Moving the tool in this way dramatically increases the machining center't access to features at different angles or on different faces of the part. A machine capable of 3+2 machining often can reach all of the machined features of the part in a single setup. True five-axis machining refers to the ability to not just position the tool along the rotary axes, but also to feed the tool through the cut using these axes. Interpolated combinations of A-axis, B-axis and linear-axis motions can allow the tool to smoothly follow a contoured surface. This type of machining has long been important in the aerospace industry, where machined parts follow the aerodynamic forms of aircraft.
Advantages of five-axis machining An important advantage of five-axis machining is the ability to cut deep features with a short cutting tool. A short tool is less prone to vibrations that could damage or shatter it during cutting. Short-tool cutting is achieved by using the A-axis to tilt the cutter away from a wall so it can be guided deep into a cavity without the shank colliding with the vertical surface. Short tools also maintain fast feedrates, a tradeoff with long cutting tools. A five-axis capability would permit a moldmaker to cut a 60mm cavity with a 30mm tool, a more stable and thus more efficient operation than with a longer version. Another example of the benefit an A-axis provides is in machining shallow surfaces with a ball-and-mill. Many moldmakers use a fixed-axis ball-and-mill for this operation. But though the center point of the tool is in contact with the surface, it usually doesn't produce a good finish because it doesn't cut as effectively as the outer edges. Running the ball-and-mill on a tilted axis would move the center of the tool away from the surface, yielding a better cut and finish. A five-axis machine can cut complicated shapes for parts like engine-turbine blades, which require toolpaths that follow undercuts and other nonlinear shapes. Even simple geometries like electronic boxes that need holes machined into them for wiring and other connections, can be finished quickly and with less labor ?and sometimes better quality ?by a cutter programmed to work on five sides without resetting the fixture.
When to use five-axis machining? Many companies simply expose different surfaces (planes) to the spindle for machining. Such would be the case on a very odd shaped workpiece that must be machined on several sides. In one sense, this kind of machining is simply an extension of what can be done with the fourth axis. If this is your area of interest, you'll want to learn more about "variable plane selection." This feature is like the standard G17, G18, and G19 (XY, XZ, YZ) plane selection commands, but it allows you to define any plane for machining. This allows you to use many of the standard programming features like canned cycles, cutter radius compensation, and axis rotation, making programming much easier.
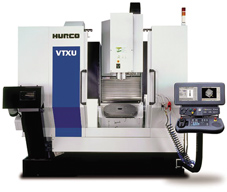
When machining elaborate 3d shapes, as would be the case with injection molds and EDM electrodes, it is important to keep the cutting tool perpendicular to the machined surface during machining. This requires five axes of motion (three linear, two rotary). Note that this kind of machining is always so sophisticated that it requires a CAM system to prepare programs, and the CAM system does all the hard work related to figu
Air Max