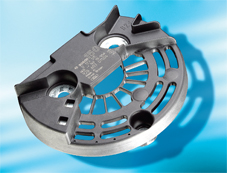
Improving properties and resitance
Source: Release Date:2009-07-13 127
Add to Favorites
The launch of Ultramid?has seen tremendous improvements in the properties of polyamides resulting in a reduction in cycle time and in the size of the injection moulding machine, as well as longer lifetime of tools.
BASF''s introduction of its Ultramid?line signifies the emergence of a new range of engineering plastics possessing improved properties. The Ultramid?high speed products include three highly filled Polyamide 66 grades: Ultramid?A3WG10 high speed, Ultramid?A3WG7 high speed and the optimum-warpage Ultramid?A3WGM53 high speed. The first two products are filled with 50% and 35% glass fibres, respectively, while the third one is filled with glass fibres and minerals. The incorporation of special nanoparticles into the plastics accounts for a marked improvement of these products not only in terms of the flow properties but also of the heat-ageing resistance at high temperatures. Currently, there are no other polyamides with this extraordinary combination of properties in the market. Depending on the glass fibre content, Ultramid?high speed flows at least twice as far as comparable standard grades. This results in a reduction of cycle time, reduction in the size of the injection moulding machine required, as well as longer lifetime of tools, thereby providing a host of costs benefits. Focusing on the needs of customers and consumers, the Ultramid?high speed products are engineered to meet the requirements of cooler end caps and ducting in turbo charging systems. In keeping with the market needs to provide high-value products that reduce part cost, Ultramid?A3W2G10 can endure a continuous temperature of 210?C, surpassing PA 66''s typical longterm useful range of 140?C - 150?C. This grade can replace more expensive resins like polyphthalamide and polyamide 46, lowering the overall part cost. Even with 50% glass reinforcement, this material has excellent processing flow properties, and provides a superior surface appearance. Vibration welding of the material is easy, allowing for the weld strength to remain high after heat aging. Ultramid?A3W2G10 also provides "metal-to-plastic" opportunities, enabling OEM''s to reduce vehicle weight, improving gas mileage and reduce emissions. Enhanced automotive parts Even before the launch of a new generation of Ultramid?High Speed products, this line has been used in highly complicated applications such as in automotive parts. The Bosch alternator cover made of Ultramid?A3UG5 LS is a plastics material being used for the first time in automotive parts due to its flame retardant properties. The product - dyed black - is rendered flame retardant without halogen or red phosphorus and it is rated V0 according to the UL 94 fire safety standard. This is the only way to properly protect the alternator while meeting the high requirements made by Bosch standard N 2580-1 governing the contents of the components. Moreover, these plastics can also be laser-written, a property that is becoming increasingly important: The logistics of large companies as well as the administration of detailed parts information often call for barcodes and data-matrix codes that can be flexibly and cost effectively applied by means of laser technology. Another example where plastics replaced the use of magnesium construction is in the Audi Q7 fitted with an airbag housing made of Ultramid? offering sufficiently elastic properties under cold conditions but also rigid enough at high temperatures, easier to process than magnesium and exhibits good flame retardant behaviour. Dual-clutch transmissions are among the most innovative automatic transmissions and another area where Ultramid?has been applied. Continental''s dual-clutch transmissions have been systematically improved over the last few years since they were first used at Volkswagen. The plastic parts of the integrated control units for these dual-clutch transmissions used at VW, Audi, Ford and BMW areAir Max 95 Invigor Print
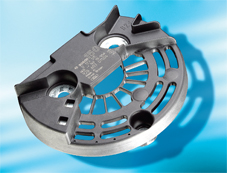
Add to Favorites
You May Like