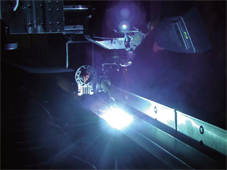
Laser welding in metalworking industry
Source: Release Date:2009-09-28 100
Add to Favorites
激光焊接在金属加工业的发展已成体系,它将若干不同材质、厚度、涂层的钢材、不锈钢材等进行焊接以形成整体板材、型材等,满足了零部
Laser welding is now a full-fledged part of the metalworking industry, whereas 20 years ago it was used primarily for unusual applications where no other welding process would be suitable. But very few manufacturing engineers have seriously considered employing lasers in their own operations. There are many reasons, but a primary one must be unfamiliarity with the operation and capabilities of a laser system. Laser welding could be used in place of many different standard processes, such as resistance (spot or seam), submerged arc, RF induction, high-frequency resistance, ultrasonic and electron- beam. While each of these techniques has established an independent niche in the manufacturing world, the versatile laser welding approach will operate efficiently and economically in many different applications. Its versatility will even permit the welding system to be used for other machining functions, such as cutting, drilling, scribing, sealing and serializing.
In this article, we will look at the advantages of laser welding for tubes, the role of gases in laser welding, and what benefits it can offer to manufacturing engineers. Advantages of laser welding for tubes Compared to classical TIG-welding, laser joining with round laser is three times as fast. The speed of the joining operation is restricted not by the power of the laser, but by the integrated annealing unit. Additionally, all usual stainless steels can be welded correctly, regardless if they are austenitic or ferritic. However, most manufacturers prefer to use laser welding for ferritic chrome steels. Ferritic steels like 1, 4509, 1, 4520 or 1, 4521 are also said to be economical and technically feasible for making pipes with, because they are both cheap and have good corrosion resistance. Laser's inherent advantages s hine when manufacturing stainless steel tubes out of these materials, because it can provide exact control of the inserted energy input per unit length. Contact-free carbon dioxide (CO2) slab laser welding is also more reliable and has greater availability compared to TIG- welding with its frequently-replaced electrodes. The CO2 slab lasers can be combined with profile welding systems, which have gap recognition and sensor technologies. This can adjust the weld to minute meanderings of position and achieve optimal welding results in difficult conditions. Laser weld seams also tend to be more resilient compared to conventionally welded seams. Role of gases in laser welding Lasers are used widely in the automotive, consumer goods manufacture, defence, aerospace, general fabrication and shipbuilding sectors. They are popular because they provide flexible, rapid and cost-effective metal component manufacturing. Unlike electron beam welding, which requires a vacuum, laser beam machining of metals takes place with a gas atmosphere in place. Given the applications of lasers, the experts have researched various parameters, such as beam energy, beam quality and focusing. The careful use of process and shielding gases can also improve quality and profitability. Metal cutting composes 85% of laser applications in the industry. One of the problems with laser cutting is the large drop in speed as the plate thickness increases. In oxygen- assisted laser cutting of mild steel of plate thicknesses above 8mm, a rapid mechanism occurs in the upper part of the plates, helped by a reaction between oxygen and iron vapor. The slower mechanism at lower depths is because the oxygen has through diffuse through liquid iron oxide because it can react with the iron at the cutting point. In laser welding, performance may be impaired because of a plasma plume which occurs in the gas above the weld. This plume absorbs the laser beam. This phenomenon can be mitigated by using a less ionisable shielding gas such as helium. If the laser beam power is lower, part ofSaldos - Entrega gratuita
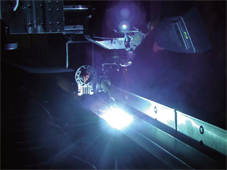
Add to Favorites
You May Like