Several types of lasers are now available for welding plastic components. With PPA resins being more suitable for a wider range of applications because of their outstanding properties, welding techniques have become highly specialised and more flexible. 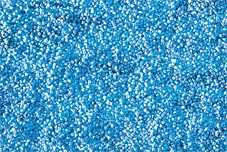
Laser welding has become a popular method of joining plastics in a wide variety of applications. This process offers a number of attractive features including: speed and efficiency; cleanliness, no debris as with vibration or ultrasonic welding; no consumables, such as adhesives; no vibration that can damage sensitive components; high bond strength; hermetic seal can be achieved; and laser equipment can be used for multiple applications. Polyphthalamide (PPA) resins are fit for a wide range of applications because of their outstanding physical, thermal and electrical properties. Unlike many other resin types, PPA resins can resist infrared soldering environments. Most Amodel ?PPA natural and black grades released by Solvay Advanced Polymers are suitable for laser welding. The company has also been supplying laser transmissive colours that are available on special requests. With a heat deflection temperature of 536癋 (280癈) and continuous use temperature of 338癋 (170癈), Amodel?PPA can deliver the thermal performance ideal for the short term as well as the long haul. It retains its exceptional mechanical properties ?strength, stiffness, fatigue and creep resistance ?over a broad temperature range and in high humidity environments. The product has the mechanical properties that are ideal for metal replacement and has excellent high-temperature capability. Aside from its outstanding electrical properties, the material is resistant to fuels, glycols and chemicals. It also has dimensional stability and low moisture absorption, as well as low vapor transmission rate. The laser welding process Laser welding typically joins two materials that differ in their response to laser radiation. One material is essentially transparent to the laser (the transmissive material) and the other absorbs the energy and melts (the absorbing material). Welding occurs when the laser energy causes the temperature of the absorbing component to increase to its melting point. Heat is transferred to the transmitting component by conduction and when it melts, the laser energy is removed and the material cools forming a strong joint. The laser energy penetrates the upper layer and is absorbed by the lower material. The molten material transfers heat to the upper layer. A molten pool forms from both layers, then the pool solidifies when it cools to form a high-strength weld. There are several types of lasers which can be used to weld plastic components. Nd:YAG lasers have the purest light and are typically the most powerful but are also the most expensive. Diode lasers are more common and less expensive. Since the light from CO2 lasers is readily absorbed by most plastics, these lasers are not used for transmissive laser welding. CO2 lasers may be used only for welding very thin films. Fibre lasers are also under development, which offer improvements in energy efficiency, although these are relatively high in cost.
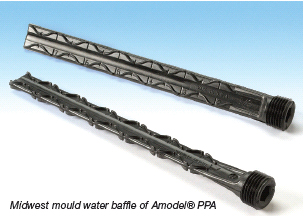
Material requirements There are specific requirements for both the absorbing and transmitting materials to be used in a transmissive laser welding application. Ideally, the base polymer comprising each component would be the same, but chemically compatible polymers with similar melt points can also be used. For example, Amodel?AS-1133 HS NT can be welded to Amodel?AS-4133 HS BK324. The transmissive component allows the laser energy to pass through it to heat the absorbing component below. Therefore, the transmissive component must be relatively transparent to laser energy at the wavelength of the laser being used. The transmissive layer will remain relatively cool while t
Brands