The blow moulding sector has been increasingly meeting the challenges in the production of PET bottles and containers through more advanced production techniques. In addition, the growing availability of automated management system has created positive impact in the design, production and overall quality of the final product.
In this area, Agr International offers a number of products that are designed to aid bottle manufacturers achieve their most aggressive light weighting and sustainability goals while maintaining the highest quality. Agr products are designed to assist container producers, converters and fillers stay competitive while meeting the increased quality demands of today’s changing world. In particular, Agr has introduced several advances in aid of PET bottle production. The company’s Process Pilot® automated blowmoulder management system – with Individual Mold Control™, is designed to help PET bottle manufacturers measure, control and optimise their bottle blowing process in order to produce the highest quality, best performing bottles possible while maximising production efficiency. The Process Pilot system interfaces with the blowmoulder to provide precise material thickness distribution on a per bottle basis while managing the blowmoulder to eliminate the effect of process and environmental variables that impact bottle material distribution throughout the production cycle.
The Process Pilot system offers a simple three-step approach towards PET blowmoulder management. The first step entails the measurement of material distribution and pearlescence on every bottle. The second step controls the blowmoulder to overcome process variation and maintain on-target material distribution. The third step optimises the process to suit the product, application or business objective of the production facility.
Not only does this system simplify and stabilise the production of PET bottles, but it also provides the versatility to manage bottle production in a manner most suitable to the product and application. Whether the goal is to make the lightest bottle possible, process preforms of mixed lineage or material quality, improve bottle shelf-life and performance characteristics, save energy or just run a stable process 24/7, the Process Pilot product group offers a means to realise this goal profitably and with confidence.
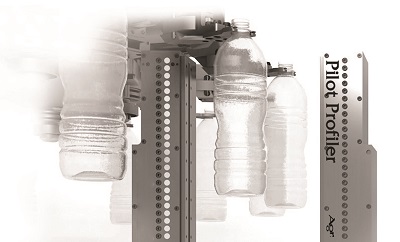
Process Pilot system, with the lightweight option
Meeting the sustainability challenge
With increasing focus on sustainability in packaging, Agr’s lightweight option for the Process Pilot blowmoulder management system gives brand owners and bottle manufactures another tool to meet this complex and growing challenge. The Process Pilot system, with the lightweight option provides assurance that the limited material available for producing a light weight PET bottle is distributed exactly where it needs to be, and at the appropriate thickness, to ensure proper performance.
There are many facets to this issue and improving the sustainability footprint of a product or brand can be a complex undertaking. Most avenues to sustainability are not under the direct control of the bottle manufacturer or brand owner. One option that is within their control however, is the reduction and optimisation of the amount of resin that is used to manufacture the bottles. Resin (or weight) reduction per bottle does not need to be excessive to have an impact with regards to sustainability and financial benefits particularly when factoring in the quantity of bottles produced over a given period of time.
Over the years, many PET bottle manufacturers have made great progress reducing excess material and moving towards lighter, more sustainable bottles. However, as weights continue to be reduced, the role of process variation and its effect on material distribution increasingly becomes a factor in the success of the weight-reduction program. The Process Pilot blowmoulder management system was developed to address this issue and offers manufacturers a valuable tool to use in their weight reduction efforts.
The Process Pilot system, with Agr Pilot Profiler® measurement technology installed inside the blowmoulder, provides a means for manufacturers to accurately measure material distribution on every bottle (to 0.05mm), in real time, and proactively adjust the blowmoulder to maintain proper distribution, countering the effect of process variation. In the push for more sustainable bottles, weights are being reduced even further and, with that, the sidewall thickness of the bottle. In order to process these bottles effectively and control the material distribution, additional measurement accuracy is required. The new Lightweight option, incorporated into the Pilot Profiler measurement component, offered with the Process Pilot system was developed to address this need for even greater measurement accuracy and control on very light bottles. With this option, a level of control is now available with the Process Pilot system that extends the measurement range to 0.025mm, with an accuracy of +0.01mm for PET bottle sidewall material. This added functionality delivers greater distribution control on bottles with very thin sidewalls or at specific locations on other types of bottles where precise material management is critical to meet performance and quality requirements. This capability removes one of the barriers to producing usable, lighter and more sustainable bottles.
Agr’s Process Pilot automated blowmoulder control systems are operating on over 400 PET bottle production lines. The Process Pilot system is unique in that it manages the blowmoulder based on direct bottle measurements, on every bottle produced. By controlling the blowmoulder based on direct feedback from bottle measurements rather than just blowmolder performance indicators, the Agr system can ensure that the final product has the desired quality and performance attributes in spite of environmental, blowmoulder or material variations that can occur during the production process. Now with the lightweight option, the process can be controlled for even the lightest bottles. The option is currently available on all new production Process Pilot systems. To achieve these capabilities on existing systems, Agr also offers an upgrade package that can be easily installed in the field.

Agr Pilot Profiler® measurement technology installed inside the blowmoulder
For greater productivity
The Agr Process Performance Optimisation Group was created to offer technical assistance to maximise the productivity and efficiency of PET blowing and beverage production lines. The Group was established to provide self-manufacturers with a go-to resource to help overcome some of the everyday challenges in producing their own bottles. The approach of the Process Group is somewhat different than what is traditionally offered by the blowmoulder manufacturers. The Agr Process group takes a holistic approach towards optimisation that not only focuses on the blowmoulder, but goes beyond to understand issues affecting the efficiency of the entire production line. Since Agr is not affiliated with any specific brand of blowmoulder, the Group can provide whole plant assistance in operations that have different blowmoulder brands in the same facility.
Some of the offerings now available through this group include working directly with a plant’s process engineers and plant floor personnel to help manage challenging light weight applications, develop effective processing recipes and address process variation and quality issues as well as a myriad of downstream process improvement efforts that can lead to improved pack rate. Agr’s consulting professionals work directly with plant personnel to ensure efficient blowmoulding and container flow downstream in order to reduce manufacturing costs.
Agr is not a novice when it comes to managing blowmoulder performance. This Process Performance Optimisation Group is an outgrowth of the Process Pilot automated blowmoulder management programme. With over 400 Process Pilot systems operating in the field, Agr system engineers have encountered many of the issues that traditionally plague PET bottle manufacturers, helping to identify a need for this kind of service. As part of the installation and commissioning of these Process Pilot systems, Agr engineers have been tasked to provide some of the very services that are now being offered through the Process Performance and Optimisation Group. However, through this group, the services have been greatly expanded and are no longer limited to facilities only using Agr’s Process Pilot system.
Air Max 90 Classic