When you think of respiratory and surgical masks, which are currently produced predominantly in Asia, ultrasonics is probably not the first thing that springs to mind. Yet ultrasonic welding plays an important roll in making these products. As an experienced technology provider for mask production equipment, Weber Ultrasonics AG now manufactures respiratory and surgical masks in Germany. This is made possible by the fast and active support of other companies as well as the huge dedication of its own employees.
Efforts to stem the spread of Covid-19 make one problem of globalisation clear: the dependency on low-cost manufacturing countries for personal protective equipment (PPE). That is why, in addition to protective clothing and gloves, breathing protection and surgical masks have been in short supply in Germany and other European countries since the global spread of the corona virus Sars CoV-2. 'Since the Sars pandemic in 2002/2003, we have been producing equipment for the manufacture of different protective masks made of nonwovens based on thermoplastic synthetics. The equipment is primarily supplied to customers in Asia,' reports Christian Unser, Chief Sales Officer at Weber Ultrasonics AG. It includes components such as generators, boosters, converters and sonotrodes as well as complete systems for welding, laminating, cutting and embossing with ultrasound. Producing masks itself was never an issue for the component and plant manufacturer based in Karlsbad (Germany) – until the start of March 2020.
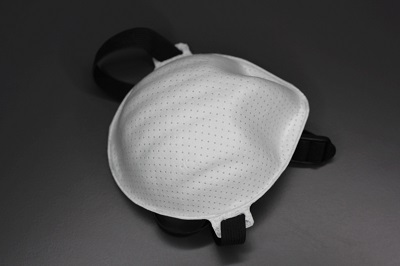
Entering into production of FFP respiratory masks
What triggered it was an enquiry from a mechanical engineering customer who was unable to get filter domes for its special ventilated respiratory masks in FFP2 protection class as a result of the export restrictions in place for these products in virtually all countries. 'Together with the customer, we developed a plant design for producing the three-dimensional filter elements in a very short time. The customer immediately placed an order for three machines,' explains Christian Unser. In parallel with this development, Weber Ultrasonics converted the design into a standard machine for the production of complete breathing protection masks. The first process step of deep-drawing the masks represented a challenge. This takes place through hot-forming, which requires a suitable tool as well as special heating elements and corresponding control units. In order to be able to produce corresponding prototypes quickly, Christian Unser turned to a market player that also works in this segment and spontaneously provided a heating element and control unit. The Head of Design at Weber Ultrasonics obtained a second one from his former employer. The necessary tool was made by a neighbouring model maker and long-standing partner of the company practically overnight. 'It really is great how different companies have offered spontaneous support and cooperation,' comments the Chief Sales Officer.
60 respiratory masks per hour with one machine
The production of the breathing protection masks takes place with this standard machine in a multi-stage process. In the first step, an open-pored fibrebond as stabiliser, a layer of meltblown nonwoven as particle filter and a layer of spun-bond are shaped through hot-forming. The edges of the masks are then joined in an ultrasonic welding process. To do this, an ultrasonic converter converts the electrical signal produced by the generator into mechanical oscillation. This is transferred via a booster and a customised welding tool, the sonotrode, onto the surface to be joined. The frictional heat this generates causes the nonwoven materials to melt specifically at the edges, where they form a permanent bond without distorting. At the same time, the reliable, energy-efficient and productive joining technology ensures a soft and skin-friendly surface. After the masks are then punched out mechanically, tapes are attached for fastening them.
The production capacity of the compact standard plant with a single tool is around 60 breathing protection masks per hour. The aim is to achieve protection class FFP3 for the masks produced according to the current standards and to perform an accelerated inspection of corona virus pandemic breathing protection masks for Germany.
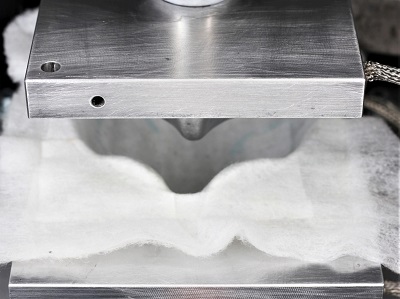
Virtual start-up with real twin for surgical masks
Weber Ultrasonics has also experienced increased demand for production equipment for surgical masks. The company's solutions in this segment so far enable the production of 200 masks per minute. 'For this application we are currently working all-out to set up a testing plant at our premises that will use a newly developed procedure for continuous ultrasonic welding. This will enable us to increase production capacity to 400, maybe even 600 masks per minute,' explains Christian Unser. This machine combines the steps of folding the fabric, integrating the nose wire, vertical and horizontal welding, welding on an elastic band and separating.
One reason for the fast implementation of this system in the factory in Karlsbad is the current travel restrictions. 'We now need to put the plants into operation virtually at our customers' premises and to do this it is important that we have the same performance here,' says Christian Unser. 'This also has the positive effect that we can push forward developments directly on the plant, perform tests for customers and above all produce surgical masks in large quantities ourselves.'
Weber Ultrasonics AG develops, produces and markets solutions and components for the industrial deployment of ultrasonic technology. It specializes in cleaning, welding and cutting with ultrasound as well as in other special fields of application. The company is certified to DIN EN ISO 9001:2008 and has already won multiple awards for exemplary corporate management. The family-run medium-sized company with HQ in Karlsbad, Germany, has 130 employees worldwide. Weber Ultrasonics AG has subsidiaries in the US and Asia, as well as Weber Entec GmbH & Co. KG, which is based in Waldbronn, Germany, and specializes in ultrasound-based technology for biogas and sewage treatment plants.
Adidas