PLASCO Engineering Inc. has been promoting its products at CHINAPLAS and without a doubt, this major exhibition has played a key role in entering the huge Asian market. Tony Wang, General Manager, was present at the company’s booth to meet exhibitors and discuss the company’s products.
As the plastics industry has been focusing on achieving the goals of Industry 4.0 for some years, CHINAPLAS 2019 has put its focus on “circular economy”, which PLASCO expects to be the next big trend. “Across various industries, the global market has been facilitating the move to a more circular economy with new policies on recycled plastics. Athletic wear from Nike and Adidas made from plastic waste has being successful for years, widely encouraged by consumers. In turn, companies such as Coca-Cola, Volvo, and Ikea have also announced its intention to increase the use of recycled plastics,” Mr. Wang said.

For many years, PLASCO has well implemented measures toward achieving a circular economy by developing extrusion line running 100% post-consumer washed PET bottle flakes, converting PET waste to commodity product such as PET bristle monofilament for broom and brush usage, as well as PET straps for packaging applications.
“PLASCO’s successful development of high permanence extrusion line has opened up new potential for recycled PET, which add an extra green touch to PLASCO’s extrusion line, and is of great economic and environmental interest,” Mr. Wang explained.
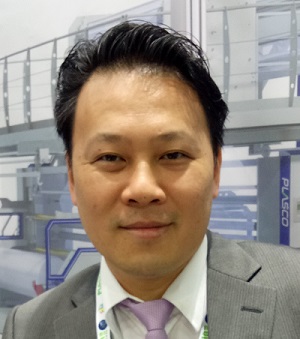
Mr. Tony Wang, General Manager, PLASCO Engineering
Versatility and efficiency combined
For more than three decades, PLASCO has being manufacturing comprehensive range of monofilament extrusion lines, providing technical solution in the field of PP, HDPE, PA, and PET monofilament production. From standard monofilament lines for all domestic application in packaging, agriculture, and fishery, to lines tailored for specific requirement for industrial and medical application, PLASCO offers the complete spectrum of possibilities.
The mechanical demand of monofilament used for technical fabrics has increased. Through PLASCO’s technical expertise and extensive experience in the field of monofilament extrusion line, the new development in bi-component (bico) monofilament extrusion was planned, developed, and was already found to be extremely versatile that it allows numerous material combinations for various applications.
Bico monofilament is manufactured by means of coextruding of two different polymers system, typically in concentric core-sheath structure, also others such has islands or side-by-side constructions.
“The bico monofilament technology brings the functionality to monofilaments. The two polymers constructed monofilament able to develop special properties achieve dimensional stability, strength, elasticity of the core as well the lower melting temperature or special surface properties of the sheath,” Mr. Wang stressed.
As a system supplier that has built its position as one of the leading monofilament extrusion lines manufacturers to the global market, PLASCO not only supplies equipment, but also provides the complete engineering and extensive knowhow in the process technology provide customers reliable and extremely efficient monofilament production to facilitate the ever-demand requirement of all market sectors.
Tomorrow's challenges
For the plastic industry, there is always concern over the environment and sustainability, global competition, and unstable raw material price. The next tier includes global exchange rate, implement of regulations and restriction, workforce shortage, and consumer perception of plastics.
Continuous development and sustainability is considered as core value to PLASCO. "We are always committed to working with customers to find sustainable solutions with our extrusion line and technology. Those perspectives vary by industry; in packaging for example, we are committed to develop extrusion line for cost effective and efficient ways producing high quality product with higher output. In agriculture and fishery industry, we are committed to develop new process technology to produce higher strength product while maintain or even lower raw material usage. For textile industry, we are committed to work with customers develop new filament product satisfy mechanical demand for technical fabrics," Mr. Wang said. Furthermore, PLASCO considers competitive intensity as good for the industry and drives greater innovation in the plastic industry. In response, PLASCO will continue to build its experience and knowledge working with suppliers and customers as it fully understands collaboration along the entire value chain is critical to success.
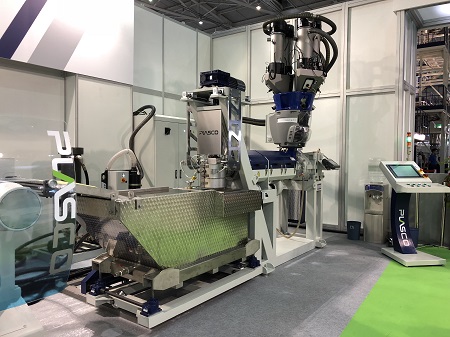
Besides these mentioned challenges, the plastic industry also faces issues such as currency fluctuations, changes in government regulations, country specific investment incentives, many of these are beyond our ability to control. What we can control is how we can innovate and design, and ultimately cost effectively and quality manufacturing.
Overall, plastics nowadays has become a major material of choice, and considered as the best solution to fulfill requirement of various applications, it offer design flexibility and many other benefits that are appreciated in many of the industries we serve. As an engineering company and manufacturer of comprehensive range of plastic extrusion line, we are very optimistic with trend of plastic industry. Furthermore, having a global presence, allows us to grow with our global value chains as stay competitive in the local environment in which we operate, we have a bright future.
For more information, visit us at www.plasco.com.tw.