As Polystar's recycling machine has gained reputation for being successful in the Japanese market, a well-known company located in Ibaraki, TOA Co Ltd, decided to go for Polystar's recycling system. Established in 1963, the customer has been purchasing post-industrial and post-consumer grade waste from all sectors including the blown film extrusion industry, food packaging film industry, injection molding and blown molding industry. The large volume of waste handled is made possible with the presence of five recycling lines in the recycler's facilities, with plans to expand business scale in the near future.
“Expansion is necessary for enterprises to survive in the long term, and ensure of sustaining sufficient market share during this fierce competition," according to Mr. Kobayashi, CEO of TOA. The Polystar customer is eyeing not only the Japanese market, but also the bigger foreign markets including the United States, UK, Korea, China, India, Thailand, Indonesia, Middle East, and Africa.
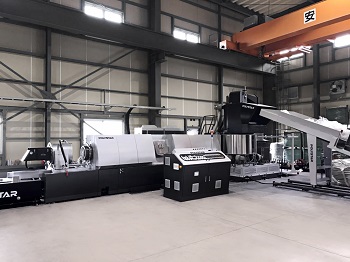
The simple and easy operation and maintenance of the machines is the key for successful recycling business. The excellent quality of the recycled pellets produced is another contribution to the business, which relatively saves the operation cost and enhances the production performance. As the customer states, Polystar truly plays an important role and performs well with its “Simple” machinery design and quality assurance.
With a new recycling hall built and the need to fill orders, the Ibaraki-based customer requested Polystar's recycling line installed in the new facility. However, due to the Covid-19 pandemic outbreak taking place from February 2020, the technical team of Polystar is prohibited to install the machine in the customer’s factory. Thanks to the simple structure design, user-friendly interface and professional on-line remote installation guidance, Polystar facilitated the successful installation of the machine to create the indispensable commercial value for both companies. Finally, an Repro Flex 150 with processing HDPE/LDPE/LLDPE film and bag scraps has stably reached 600~650 kg/hr capacity at the customer's new factory. The excellent quality recycled pellets prdouced by the machine are mainly sold to the big film/bag producers and used in shrink and construction film production as well as for intermediate layers in laminated films.
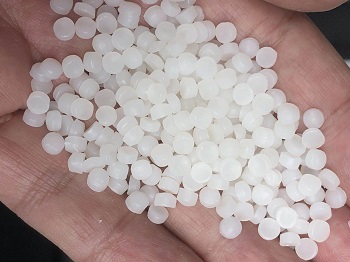
The factory manager indicated that the size uniformity of recycled pellets is the critical point related to the homogeneous level and quality of the final product. By utilizing Polystar's intelligent pelletizing system and the patented air cylinder pressure control technology, it significantly stabilizes the quality of the recycled pellets and enhances the level of production automation. With Polystar's latest intelligent pelletizing system and corresponding air cylinder pelletizing pressure control technology, the reliability and uniformity of the recycled pellets is ensured, and profit is significantly increased.
Apart from the recycling business, the customer also utilizes the recycled pellets back to the production line for housewares, such as the patented sonic driver for toothbrush, etc. "We aim to recycle every possible plastic waste and convert it into useful materials in order to protect our environment. Polystar's simple but powerful machinery design concept had been affirmed by global customers and professional on-time services are the decisive criteria for our long-terms cooperation," Mr. Kobayashi concluded.