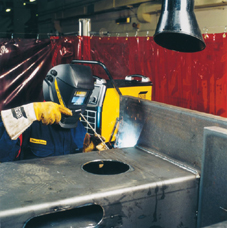
Problems in arc welding designs
Source: Release Date:2009-06-18 137
Add to Favorites
焊接中所产生的缺陷或断点会对产品的性能及寿命带来较大影响。本文将着力于此,为您介绍电弧焊中产生的普遍缺陷以及应对策略。
Welding discontinuities can affect product performance and longevity. Understanding carefully the various defects, their causes, severity and remedies can help ensure high-quality and superior performance. This article presents an overview of welding defects and provides design strategies to help prevent them. Quality design measures A weldment's service performance is generally identified at the design stage. This is the time to decide what materials can be used according to accepted specifications and considerations in the mechanical properties guaranteed in the finished construction.
This stage gives the designer's opportunity to select joint types that will transmit the service stresses successfully, noting the inevitable imperfections produced by the welding processes are at an acceptable level and controlled. The designer must establish precise criteria for any possible imperfection in the manufacturing to identify clearly what size discontinuities must be repaired or rejected. Economy and manufacturing costs, including the weld dimensions, the amount of filler metal to be deposited, and the suitability of the process employed, are weighed, knowingly or unwittingly, at the drawing board. Joint design and weld details have a major effect on the fatigue life of structural elements. Fatigue is the formation and propagation of cracks, leading to fracture, under fluctuating stresses of limited intensity that would not be harmful if they were static. An expert designer knows how to prevent discontinuities and sudden geometric changes that can cause stress to rise locally and initiate cracks. The exact location and the magnitude of stress concentration in welded joints depend on the joint's design and load direction. Welding joints, discontinuities Common weld types are butt, T, corner, lap and edge. These may be defined as square, bevel or special groove; fillet and simple if they are welded from one side only or double if from both sides. Sometimes improper condition can render a manufactured welded structure imperfect. A lack of local physical material continuity at or near the weld is called a discontinuity or flaw. Such a feature has to be checked and evaluated to identify if it is a harmless imperfection or an intolerable defect that must be removed because of the service the structure will sustain in operation. Possible rare unintentional load or temperature overrun caused by unrelated equipment malfunctions also must be considered. When seen, discontinuities should always be assessed. Detection techniques need be sensitive enough to check harmful or reject indications only. An oversensitive nondestructive inspection technique is not an advantage, however. In fact, it may be dangerous because the presence of too many irrelevant indications can mask those few, but harmful discontinuities that have to be evaluated and eliminated. Obvious imperfections A defect is nothing more than an excessive discontinuity. It is determined by design acceptance/rejection requirements based on past experience or more modernized criteria of fitness for service and calculated using the rules of fracture mechanics. Fitness for service is a concept that enables individual flaws to be assessed and allows the designer or the operator to decide whether or not to repair. Fracture mechanics is a method of quantitative analysis, a numerical computation procedure for evaluating structural behavior (fracture instability) in terms of applied stress, crack size and shape, and specimen or structure component geometry. Different approaches exist for calculating maximum acceptable flaw dimension according to fitness for service principles. These approaches are formally presented in codes; some have already been used widely. Common weld troubles Discontinuities are commonly grouped based on geometric characteristics. CrackRacing Archives
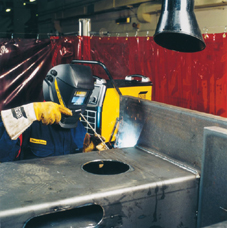
Add to Favorites
You May Like