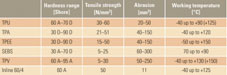
Special material
Thermoplastic elastomers are mainly used for the extrusion of spiral hoses. This material class combines the elastic properties of elastomers with the processing advantages of thermoplastics. In principle, this unique material combination can be obtained by the following procedures: ■ During mixing of a thermoplastic with an elastomer, the thermoplastic forms a continuous phase, in which the elastomer constituents are finely distributed. Included in this material group are e. g. thermoplastic vulcanizates, thermoplastic olefin elastomers (TPO), etc. ■ If elastic and thermoplastic elements are combined in a molecular chain, the thermoplastic elements create physical linking points, which permit thermoplastic processing above their softening points. Included in this material class are e. g. thermoplastic polyurethanes (TPU), thermoplastic copolyesters (TPC, also TPEE), etc. When comparing the properties of the most important thermoplastic elastomers, it becomes clear that TPU is best suited for use in spiral hoses (Table 1).Thermoplastic polyurethanes belong to the block copolymers. Their molecular structures are formed by means of poly addition using long-chained dienes, diisocyanates, and short-chained dienes.Hard and soft segments are created, which consist of different chemical structures and must exhibit a certain incompatibility. In this way, TPUs combine high elasticity with low abrasion to provide outstanding mechanical strength in a wide temperature range. In-depth knowledge about the properties and the behavior of thermoplastic elastomers were the starting point for development of the new, seamless smooth hose class. During the patented manufacturing process, the individual components for the inner and outer wall layers combine permanently into a firm material. Suitable material combinations of the two components permit the hose to be adapted to the most varied application areas.Alternative to rubber hoses
Previously, rubber hoses were considered as the cheapest and technically best solutions for conveying bulk materials. But now, the seamless conline hose sets new standards in the area of plastic hoses when compared with rubber hoses. The suction and conveying hose waster-PUR Inline 60/4 was specially developed as the first standard product for the bulk goods industry. For these applications, the demands placed on hoses for conveying abrasive and corrosive media are aimed at cutting operating costs by means of longer service life, thus leading to longer inspection intervals and reduced stocks of spare parts. In addition, properties such as low weight and easy handling are required. Tests conducted according to DIN 53516 in the manufacturer's laboratory have shown that under comparable conditions, the Inline hose will last at least 5.5 times longer than the best rubber hose that was tested (Table 2).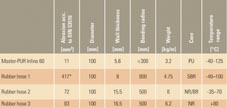