在今天的金属加工业,从高碳钢到陶瓷和钻石的各种工具材料被用作了切削工具,因此,知道工具材料之间的差别、这些差别是什么、以及每种材料的正确用途都是重要的。切削工具使用者不应忽视工具材料技术领域所取得的持续变化和进步。无论何时需要或预期要更换工具,都应当在为作业选择工具之前比较性能。切削工具必须具有硬度、韧度和耐磨性等特征。
In today's metalworking industry, various kinds of tool materials ranging from high-carbon steel to ceramics and diamonds are used as cutting tools, and because of this it is important to be aware of the differences among tool materials, what these differences are, and the correct application for each type of material. The constant changes and advancements made in the field of tool-material technology should not be ignored by cutting-tool users. A performance comparison should be made before choosing the tool for the job whenever a tool change is needed or anticipated. A cutting tool must have the following characteristics: hardness, toughness and wear resistance. Hardness and strength of the cutting tool must be maintained at elevated temperatures also called hot hardness. Toughness of cutting tools is needed so that tools don抰 chip or fracture, especially during interrupted cutting operations. Wear resistance means the attainment of acceptable tool life before tools need to be replaced.
Carbon tool steels and cast alloys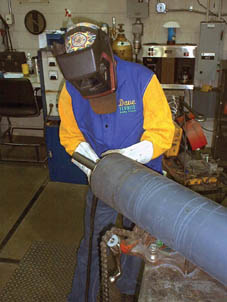
Plain carbon tool steel is the oldest of the tool materials dating back hundreds of years. In simple terms it is a high carbon steel, which contains about 1.05 percent carbon. Since it is quickly over tempered or softened at relatively low cutting temperatures of 300 to 500 F, it is now rarely used as cutting tool material except in files, saw blades and chisels. The need for tool materials that could withstand increased cutting speeds and temperatures led to the development of high-speed tool steels (HSS). The major difference between HSS and plain high-carbon steel is the addition of alloying elements to harden and strengthen the steel and make it more resistant to heat (hot hardness). Many surface treatments have been developed in an attempt to extend tool life, to reduce power consumption, and to control other factors which affect operating conditions and costs. One of the more recent developments in coatings for high-speed steel is titanium nitride by the physical vapor deposition (PVD) method. Metallurgical researchers developed cast alloys to improve cutting properties sufficiently. The principal alloying elements in high-speed steel is cobalt, chromium and tungsten. When applying cast-alloy tools, their brittleness should be kept in mind and sufficient support should be provided at all times. Cast alloys provide high abrasion-resistance and are thus useful for cutting scaly materials or those with hard inclusions.
Tungsten carbide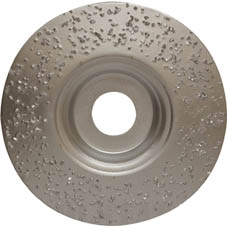
Tungsten carbide was disc
Mujer