Just as how capable mobiles devices are in doing more than sending texts of making calls, cars of today can do a lot more than just park and drive. For the last century, the car culture has become widespread in the world. In 2018, more than 70 million cars were produced with China, Japan, and Germany being the largest producers of passenger vehicles. Given the scenario, many new developments are breaking barriers to provide important changes in vehicle and automotive parts production. The automotive industry has worked in partnership with known technology companies in order to deliver the most advanced and sustainable vehicles without sacrificing comfort and safety. Thus, cars have become huge smart devices with state-of-the-art advanced emergency braking capabilities, mapping technology for autonomous driving, and better fuel efficiency. This is a driver of change to the world’s transportation trend.
Next-generation interior applications
The Renolit Group, a known globally-active specialist for high-quality plastic films, sheets, and other plastic products, has taken over the thermoforming and automotive extrusion market as they came up with a glass fibre that is 100% recyclable, which could be used for automotive interior applications. Not only is it a very commendable contribution to the current environmental problem that the world is experiencing, but it also allows a more efficient production of goods by lowering the costs, hence attracting OEM automotive buyers. Environmental imperatives and safety requirements are two critical issues facing the automotive industry worldwide. Tight emission standards and stringent regulations have compelled automobile OEMs to seek alternative methods of vehicular weight reduction in order to improve efficiency.
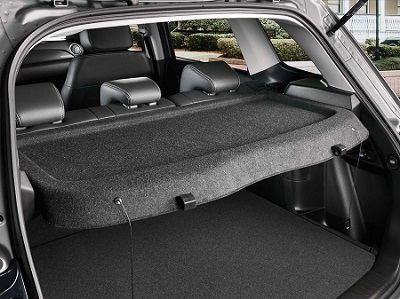
Renolit Tecnogor is a safe, 100% recyclable glass fibre reinforced thermoplastic composite.
Renolit Tegnogor continuously stands out as it is of high quality, of superior performance, lightweight, and its winning trait, being a glue-free, one-step-process material. This is done through the glass fibres being completely embedded in the PP polymer matrix during extrusion. Consequently, there are no free floating fibres in the air or exposed glass fibres in the moulding, producing safe to handle finished trim parts with smooth surfaces and edges. For reducing cut-off trim, customised blanks are typically provided, which are supplied as standard with a highly compatible film for thermally bonding textiles or other skin materials. According to a published technical data sheet for the Type A grade, the mechanical properties of Renolit Tecnogor include: Flexural Modulus (Norm I.S.O. 178) of L. ≥ 8200 N/mm2 , T. ≥ 3200 N/mm2 ; Charpy Impact Strength (Norm I.S.O. 179) of L. ≥ 17 KJ/m², T. ≥ 15 KJ/m² ; Heat Deflection Temperature, HDT (Norm I.S.O. 75A) of L. ≥ 145 °C, T. ≥ 120 °C. The exceptional and patented PP/GF composition and extrusion process used by Renolit composites production lines from Italy created the superior performance.
The added value technical support, process, and application knowhow of the Renolit composites team benefits its customers. Francesco Maffione, the Sales Manager for Automotive Products for Renolit said that their approach is to work closely with Tier 1 convertors and automotive OEMs. This is through developing wide knowledge and network to help customers produce thermoformed parts at lower cost and higher productivity levels. Moreover, Renolit continues to look for methods to achieve higher machine utilisation, reduce process steps, decrease changeovers and cut production cycle times. Mr. Maffione also stated that Renolit gets involved in new product development projects, providing rapid technical support, which includes providing test material produced on in-house prototyping thermoforming line.
Transforming e-Mobility
Henkel drives transformation from traditional engines to electrified powertrains. Its portfolio is a combination of existing and new technologies to enable cost-efficient large-scale assembly and lifetime protection of battery architectures. Environmental regulations, such as strict regulatory fleet consumption and CO2 emission targets, are influencing the directions of Henkel in its innovations. The integration and protection of batteries and electronic components play a vital role with tonnes of new EV models being designed and launched rapidly.
Henkel has recognised three major challenges for battery manufacturers. First, as the value per battery kWh continues to be a significant commercial challenge, materials and adhesives applied in the assembly process of hundreds to thousands of cells in the battery pack need to provide high-speed curing and short cycle times. Second, for operational safety, solutions must comply with thermal management requirements as well as the UL94 flammability standard. Lastly, to ensure lifetime performance of EVs, the battery pack housing requires technologies that will allow it to be reopened. Frank Kerstan, the Director e-Mobility & Powertrain at Henkel, stated that innovative adhesive products and engineering services are playing a major role in optimising the cost-efficient assembly, operational safety and lifetime protection of battery cells. Furthermore, a good number of OEMs in 2019 are launching EV models that have been designed and assembled with its technology.
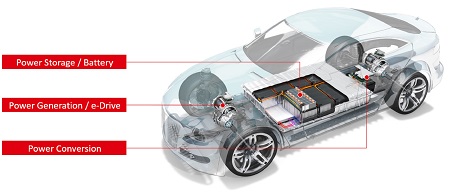
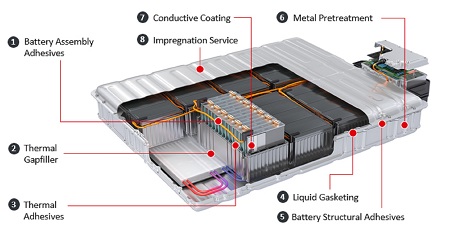
Henkel’s Loctite AA 3525 cures on demand with UV light within less than 15 seconds. Teroson MS 9396 is ideal for battery cell-to-cell bonding and battery case sealing. This modified-silane, easy-to-use one-component technology is environmentally-friendly, non-solvent and non-silicone based. With proven performance of high temperature resistance up to 100°C and excellent elongation rate of 200%, it ensures a stable and safe performance of the battery cells.
Another development from Henkel is the thermally conductive silicone-free material with 3 W/mK performs under the harshest environmental conditions. Its cure-in-place kinetics guarantees gap stability and robustness over lifetime. The unique rheology allows extremely fast dispensing for reduced processing times, decreased assembly forces and significant stress relieve for the battery cells and modules. Furthermore, the new filler technology with very low abrasiveness characteristics results in less maintenance to the dispensing equipment.
To ensure safe and efficient thermal management of the battery cells and modules, thermal conductive adhesives such as Loctite UK 6800 and Loctite EA 9794 allow efficient heat transfer to cooling plates. The two-component polyurethane technology of Loctite UK 6800 has a thermal conductivity of 1.9 W/mK. To overcome different coefficients of thermal expansion, it also offers excellent adhesion on different substrates with a shear strength of > 10 MPa and high elongation of 44%.
In order to meet the UL94 flammability standard, Teroson MS 939 FR has proven itself to be a reliable and high-performance technology. Likewise, Loctite SI 5970 acts as a custom-fit solution when it comes to resistance against oils and other automotive fluids. For the challenge of serviceability, Loctite AA 5884 (Asia: 5883) is a fast, UV light curing polyacrylate technology that provides sealing reliability by compression while allowing the battery pack housing to be reopened for repair.
Adidas Athletics 24/7 Trainer