The aerospace industry is constantly searching for stiff, strong, lightweight materials that can handle rapid temperature changes, broad chemical exposure, and provide long service life with excellent fatigue resistance. Thanks to the successful launch of composites-intensive aircraft like the 787 Dreamliner from The Boeing Co. in 2011 and the A350 XWB from Airbus SE in 2015, the use of composite materials has grown significantly on commercial aircraft owing to their ability to reduce mass, lower fuel consumption and maintenance, and improve corrosion and fatigue resistance. To better support customers in the U.S. aviation/aerospace segment, Sumitomo Chemical Co. Ltd. (Tokyo) has developed two new grades of epoxy resin with enhanced viscosity for easier processing, as well as a new grade of a polyethersulfone (PES) additive to boost fracture toughness and microcrack resistance for carbon fiber-reinforced epoxy composites.
To support the aerospace industry needs for carbon composites with high performance and greater productivity, Sumitomo Chemical has developed two new grades of epoxy resin for use in prepreg production. Versus the standard aerospace grade — Sumi-Epoxy™ ELM 434 with a viscosity of 11,900 mPa-s — the new -434L grade has a viscosity of 8,200 mPa-s and the new 434VL grade has a viscosity of 5,100 mPa-s. Sumitomo also offers two higher-temperature grades (Sumi-Epoxy ELM-100 and 100H), which both have a Tg of 260°C vs. the standard 230°C of ELM-434.
Sumitomo also has expanded its offering of SumikaExcel™ PES micron-powder tougheners for epoxy composites. In addition to its standard grade of SumikaExcel 5003P, a new lower molecular weight 2603P grade has been introduced. The standard 5003P grade has a viscosity of 0.52 dl/g vs. a reduced viscosity of 0.26 for the new 2603P grade (both measured as 1% PES in N,N-dimethylformamide (DMF) solution @ 25°C). The molecular weight (Mw) of 5003P is 42,000 vs. 16,000 for the 2603P grade. Additionally, the Tg of 5003P is 227°C vs. 220°C for 2603P as measured with a differential scanning calorimeter. The new 2603P grade also features more terminal -OH groups vs. the standard grade (4.5 vs. 1.1 per 100 units).
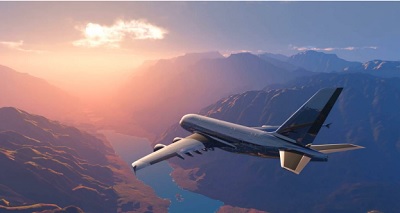
SumikaExcel 2603P, a lower-viscosity PES additive, benefits aerospace composites where the viscosity of the combined epoxy/PES matrix is highly dependent on the molecular weight of the PES even at low letdown ratios. While the original SumikaExcel 5003P additive is effective at improving fracture toughness in epoxy composites, it was not always easy for formulators to add as much additive as desired due to the high viscosity of the combined resin system — especially during prepreg production. By opting to use the lower-viscosity 2603P grade, formulators can now increase the ratio of PES to epoxy to further improve toughness of the final composite. Or, formulators can add additional polymers and additives to further modify functional properties of the composite. Yet another option is that formulators can choose one of the new lower-viscosity Sumi-Epoxy grades rather than use a lower molecular weight PES in order to drive down the viscosity of the combined polymer matrix.
Epoxies are thermoset polymers known for their thermal and chemical resistance, electrical resistivity, and high mechanical properties — particularly when reinforced with fibers like carbon, aramid, boron, or glass. Easily modified via mineral fillers, reinforcing fibers, adhesion promotors, viscosity reducers, viscosity thickeners, colorants, accelerators, plasticizers, co-reactants, and more, epoxies can be formulated to provide a broad range of properties that enables their use in a wide range of applications — from high-performance paints and coatings and structural adhesives to tooling to form plastic and composite parts, structural composites for the wind-energy, automotive, marine, and aviation/aerospace industries, and electronic components (from circuit boards to semi-conductor encapsulants and potting compounds for transformers and inductors).
PES is an amber-transparent, amorphous engineering thermoplastic known for its high temperature capabilities, high strength and impact resistance, excellent creep resistance at elevated temperatures and loads, very-good dimensional stability, low coefficient of linear thermal expansion (CLTE) over a broad temperature range, inherent flame retardance, low smoke, minimal outgasing, good and broad chemical resistance, and resistance to hot water. It is offered pelletized for injection molding, extrusion, and film processes and in powder form for cast films, filtration membranes, and as an additive for epoxy-based composites, high-temperature paints/coatings, and adhesives. PES materials are used in the aerospace, automotive, electrical/electronics, medical-device, and food-handling industries.
When ground to a micron-powder, PES has proven to be a very-effective additive for boosting the fracture toughness and microcrack resistance of epoxy composites — both in prepreg form and as a polymer for resin-transfer molding (RTM). It provides these properties over a broad temperature range without negatively affecting dimensional stability, flame/smoke/toxicity (FST), creep resistance, modulus, impact strength, or yield strength. In its role as a functional additive for epoxy composites, specific PES grades with hydroxyl (-OH) end groups react with glycidyl groups on the epoxy matrix to form a cross-linked, interpenetrating polymer network (IPN). Even though the additive is typically used at low letdown ratios of 2-12 wt-%, it adds greater flexibility to the IPN, which in turn boosts the toughness of the epoxy composite. PES typically has a glass-transition temperature (Tg) of 225-230°C, which is higher than that of aerospace-grade epoxies that average 120-200°C. Since the PES additive also has good stiffness and strength, it improves impact and crack resistance without compromising other thermo-mechanical properties. Especially important for aerospace applications, it does all this without affecting FST or the ability to mold and hold very-tight tolerances. Although it is most commonly used with high-performance carbon fiber-reinforced epoxy composites, it is equally effective in glass-, aramid-, or basalt-reinforced epoxy too.
Sumitomo can customize both its epoxy and PES grades (and even provide the PES additive in its epoxy grades) to meet specific customer requirements for processability and functionality.
Sumitomo Chemical is the world’s sole PES manufacturer that maintains dedicated PES polymerization facilities (in Chiba and Ehime, Japan) and also dedicated micron-powder grinding facilities on three continents. This eliminates the possibility of cross-contamination with other polymers — a critical and highly enforced requirement in the aerospace and medical-device industries — and it also simplifies the supply chain for processors and OEMs. Powders as fine as 15 mm and as coarse as 500 mm are available.
NEW BALANCE