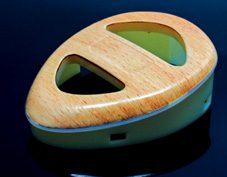
What would a sports car be without that cool look in the interior? For plastics processors, surfaces in automobile interiors have a special role. The car buyer perceives them as a visible and tactile sign of quality and, consequently, the expectations are rising among automakers and their customers. These include more functionality and design freedom. In view of these specification requirements and the increased number of vehicle models, two techniques have developed based on the IML approach (In-Mold Labeling) that can be used to create high-class metal and real wood surfaces on plastic components.
Foil technology simplifies selective electroplating Chrome-plated decorative elements in the cockpit or on the door are not only visually appealing. The metallic surfaces feel pleasantly cool. However, plastic is usually hidden underneath. Chromium, ruthenium or other materials are deposited onto a component in a micrometer-thin layer by means of electroplating. To date, this was technically challenging and costly when only a portion of a component, not the entire component, had to be metalized. With the new process called folioPlate, this can be accomplished more exactly and efficiently than previously. The process benefits from the precision of the foil technology employed for in-mold labeling (IML): A plastic foil is shaped to match the required part geometry, punched out with the correct contour and then placed in the injection mold. Plastic flowing in behind the foil forms a permanent bond with it, and the foil becomes the appearance surface of the component. At locations where the foil was trimmed or has had openings punched out, the plastic itself forms the surface. As a result, extremely sharp demarcation between regions with and without the foil is possible. While the foil is printed with a colored motif in the conventional IML process, it serves as a carrier for the metal layer in the folioPlate process. The fact that not all plastics can be metalized equally well is also exploited. ABS is best-suited, since it offers a substrate with adequate adhesion properties. In contrast PC cannot be metalized using the standard process. Used in an IML injection mold, the combination of an ABS foil and PC component permits precise demarcation between the subsequently metal-plated and non-plated regions on the finished plastic part (Fig. 1).
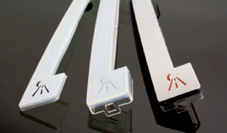
This represents a major advantage over the processes employed previously for selective plating: masking and two-component molding. With the masking technique, individual regions are covered by means of a coating or solid mask. Both must then be removed after electroplating - assuming, of course, that the part geometry permits attachment of masks in the first place. Like the new process, two-component molding combines a plateable and a nonplateable material. This approach, however, requires a sufficiently large contact surface in order to achieve a firm bond between the two materials. With current mold and injection molding technology, it is hardly possible to attach millimeter-sized snap hooks of PC to a component of ABS. Thus, they are usually produced from the same plateable material. Since plastics become brittle when electroplated, it would be ideal if these purely functional parts could be kept metal-free (Fig. 2).
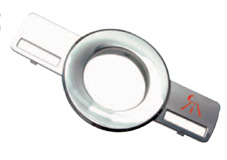
A second major drawback of conventional two-component molding is the cost structure. A two-component mold is considerably more expensive than a single-material mold. Moreover, it requires an injection molding machine with two injection units, which means a higher purchase price or hourly rate. A standard injection molding machines suffices for the folioPlate process, however.
Combining function and design Where the molded component is subjected to a high level of mechanical stress, high-st
New Balance Popular Collection